- Přehledy IS
- APS (20)
- BPM - procesní řízení (23)
- Cloud computing (IaaS) (10)
- Cloud computing (SaaS) (32)
- CRM (52)
- DMS/ECM - správa dokumentů (20)
- EAM (17)
- Ekonomické systémy (68)
- ERP (76)
- HRM (28)
- ITSM (6)
- MES (34)
- Řízení výroby (36)
- WMS (29)
- Dodavatelé IT služeb a řešení
- Datová centra (25)
- Dodavatelé CAD/CAM/PLM/BIM... (41)
- Dodavatelé CRM (38)
- Dodavatelé DW-BI (50)
- Dodavatelé ERP (68)
- Informační bezpečnost (50)
- IT řešení pro logistiku (45)
- IT řešení pro stavebnictví (26)
- Řešení pro veřejný a státní sektor (27)


















![]() | Přihlaste se k odběru zpravodaje SystemNEWS na LinkedIn, který každý týden přináší výběr článků z oblasti podnikové informatiky | |
![]() | ||
Efektivní výroba je klíčem k úspěchu
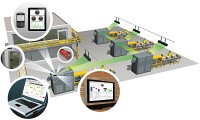


Každodenně musí management výrobních závodů, ať již na střední nebo vyšší úrovni, řešit problémy či zlepšovat postupy spojené s výkonností dělníků, správným vykazováním práce, využitím strojů, zmetky a malou výtěžností, aktuálností a přesností produkčních dat, nadměrnými prostoji, správností pracovních norem, operativností údržby či dohledem nad různorodým výrobním parkem. Jedním ze základních kritérií, které v sobě zohledňují výše uvedené faktory a indikují stav výroby, je celková efektivita zařízení, parametr OEE (overall equipment effectiveness). Kdy hodnot parametru OEE 0,85 (85 %) dosahují opravdu jen špičkové světové podniky a za dobrý či „realistický“ ukazatel v běžných podnicích lze považovat parametr OEE nad 0,6 až 0,65.
Hodnota parametru OEE by měl být jeden z klíčových výrobních ukazatelů pro vrcholový management výrobních podniků, neboť jeho hodnota má přímou vazbu na náklady výroby, a tedy i zisk firmy. Z tohoto důvodu by měl být ze strany managementu kladen důraz na co nejpřesnější hodnotu skutečného OEE.
Z praktického hlediska pak existují dva základní způsoby, jak zvyšovat produktivitu: vyrábět rychleji a méně často stát. Toto je možné pouze tehdy, pokud máme k dispozici jasné informace o výrobě, jejích ztrátách a jsme schopni je identifikovat a měřit.
Sběr dat a „strojová skutečnost“
Dnešní trh nabízí celou řadu řešení, která jsou určená pro monitoring a řízení výkonnosti výroby v reálném čase, ať již se jedná o softwarová krabicová řešení s využitím standardizovaných hardwarových prostředků, nebo nezávislé kompaktní systémy, kdy softwarové a hardwarové prostředky tvoří jeden celek – za obě skupiny lze jmenovat například řešení od společností Shoplogix, Wonderware, Rockwell Software, Papouch a další.
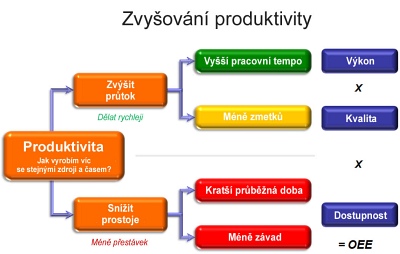
Všechna tato řešení směřují k přesnému, a hlavně nezávislému sběru dat a monitoringu „strojové skutečnosti“ jako nutného podkladu pro realistické vyhodnocení efektivity výroby. Toto je realizováno obvykle přímým vyčítáním z COM portu výrobního zařízení, monitoringem fyzických signálů nebo přepočtem z dostupných dat – vše se uskutečňuje na pozadí výroby bez zásahu obsluhy, vstupu lidského faktoru.
Ručně získávaná data, obvykle pořizovaná přímo operátorem, na jejichž zá¬kladě se přijímají pro podnik důležitá rozhodnutí, jsou často nepřesná a velmi pravděpodobně i neaktuální ve chvíli, kdy se použijí jako vstup pro nějaký analytický nástroj, ať už je to podnikový informační systém (ERP, enterprise resource planning), dílenský výrobní systém (MES, manufacturing execution system) nebo třeba jenom tabulkový procesor. I při maximální možné snaze je pak výsledkem to, že přijatá rozhodnutí jsou zcela chybná, naprosto neproduktivně využívají zdroje a plýtvají penězi.
Vezměme si třeba zde vyobrazený příklad. Přestože se v daném pracovním cyklu vyrobilo jen šedesát procent plánované produkce, ručně posbíraná data ukazují, že stroj běžel po více než 75 procent celkové doby. Z toho by vyplývalo, že nedosahoval předpokládané rychlosti (výkonu) a tím vzniklo zpoždění proti plánu. Ve skutečnosti se ovšem doba využití stroje těmto 75 procentům ani nepřiblížila, doopravdy systém zaregistroval dobu běhu jen těsně nad polovinu celkového času. Vyzbrojen touto informací, poznal příslušný tým pověřený péčí o systematické zdokonalování výroby, že musí hledat příčinu prostojů a nemarnit čas zbytečnými pokusy o urychlení práce daného stroje.
Vhodně navržený systém sledování efektivity výroby provádí základní měření a poskytuje údaje například pro firemní program systematického zdokonalování. Tím, že eliminuje nepřesnosti a zároveň zdlouhavost v získávání ručně zadávaných dat, zajišťuje strojovou skutečnost (metodika OEE používá pojem machine truth) a umožňuje provádět kvantifikovatelná zlepšení.
Vytvořený obraz
Sběr přesných dat je samozřejmě jen první částí problému. Druhou částí je schopnost tato data analyzovat, interpretovat a převádět je na užitečné informace. Dobře navržený systém sledování efektivity výroby data nejen sbírá, ale vytváří z nich také praktické a působivé reporty, a to hned po instalaci, bez nároků na jakoukoli spoluúčast IT podniku, obvykle formou grafických nebo tabulkových reportů.
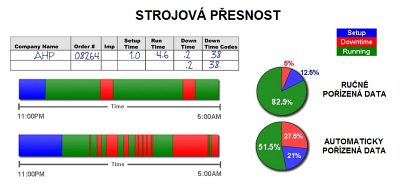
Očekávaným výstupem takovéhoto systému je pak počet výrobků, časový snímek výroby, míra zmetků, procento ztrát, příčiny prostojů a jejich četnost, rozdíly mezi směnami nebo klíčové parametry výkonnosti (KPI).
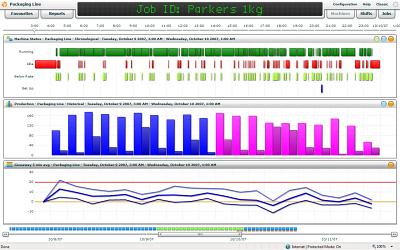
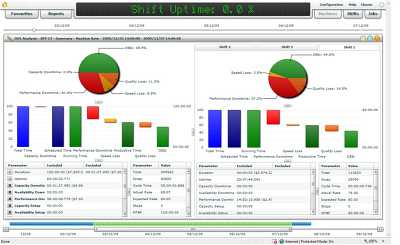
Grafické výstupy obsahují intuitivní informace, které jsou potřebné k provádění žádoucích změn, k efek¬tivnímu řízení výroby a k automatizovanému upozorňování vedoucích pracovníků na potenciálně škodlivé situace, včetně eskalační procesů.
Pro dnešní aplikace je již samozřejmostí plně grafické prostředí a možnost vnořování, získávání konkrétního detailu v rámci jednotlivých reportů, jejich tisk či export do kancelářských aplikací stejně jako dostupnost vybraných dat na mobilních zařízeních (PDA, smartphone, tablet). Takto je managementu umožněno učinit adekvátní a včasná rozhodnutí.
Angažovanost dělníků
Další, a jednou z nejdůležitějších součástí řešení je způsob, jakým systém sledování efektivity výroby zapojuje dělníky do procesu systematického zdokonalování a optimalizace výroby. Efektivnost vysoce nákladných zařízení často závisí na lidech, a proto dobře navržený systém sledování efektivity výroby musí poskytovat dělníkům, údržbářům, mistrům a manažerům okamžitou zpětnou vazbu a úplný přehled o stavu výroby a výrobních událostech.
Adekvátní zpětná vazba může být realizována pomocí různých technických prostředků – LED dispeje, TXT displeje, panelu IPC, operátorského panelu nebo jen optickou signalizací – ale vždy musí operátorům poskytovat jednoduchá a srozumitelná data a být umístěna v těsné blízkosti každého operátorského pracoviště nebo výrobního zařízení.
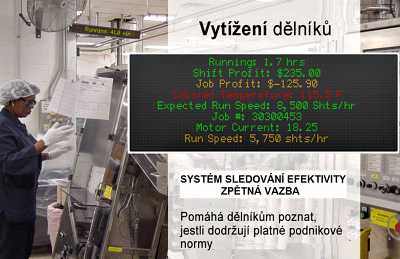
Nejenže tak zaměstnanci dostávají standardní produkční informace, ale i informace vysvětlující jim výrobní problémy či nestandardy, jako například nedostatek materiálu ke zpracování, negativní trend kritické proměnné. Díky zpětné vazbě ale mohou zaměstnanci také podle toho hned náležitě zareagovat a sami podniknout potřebná opatření, dříve než příležitost k nápravě pomine a promění se jen v historickou příčinu konkrétního nedodržení daného plánu. Takové zvýšení pravomoci pracovníků také spoluvytváří jejich poměr k procesu zdokonalování a soutěživosti, buď mezi směnami, nebo prostě ve formě snahy překonat vlastní včerejší výkon.
Dostupnost a přínosy systému
Obrovským přínosem osvědčených systémů bývá rovněž rychlost implementace, která se pohybuje v jednotkách dnů a vyžaduje minimální spolupráci ze strany zákazníka. Navíc ověřená řešení mívají návratnost kratší než jeden rok, což je z pohledu dnešní ekonomické situace výrobních podniků jistě zajímavý údaj.
Systém sledování efektivity výroby a jeho vhodná implementace dokážou být přínosem v těchto oblastech:
- přesná a neovlivnitelná data o výrobě a jejím průběhu (časový snímek výroby), minimalizace „lidského faktoru“,
- snížení nákladů na sběr dat o produkci a prostojích,
- zvýšení efektivity výroby a sledování efektivity v reálném čase,
- přesné určení skutečné příčiny prostojů,
- odhalení skryté kapacity výroby, rychlá identifikace problémů, úzkých míst a nestandardů ve výrobě,
- optimalizace intervalů údržby, parametr OEE bývá součástí programu TPM (total productive maintenance – údržba zaměřená na komplexní produktivitu),
- standardizovaná metodika – výpočet parametru OEE, možnost uživatelské definice vzorce a parametrů,
- možnost monitoringu kritických proměnných a nastavení alarmových úrovní,
- možnost definice víceúrovňového eskalačního procesu (SMS, e-mail),
- dostupnost dat v elektronické podobě ve výrobě i mimo výrobu.
Jaroslav Střelka
Autor je manažerem SWD-MES ve společnosti S&T CZ.


Formulář pro přidání akce