- Přehledy IS
- APS (20)
- BPM - procesní řízení (23)
- Cloud computing (IaaS) (10)
- Cloud computing (SaaS) (32)
- CRM (52)
- DMS/ECM - správa dokumentů (20)
- EAM (17)
- Ekonomické systémy (68)
- ERP (76)
- HRM (28)
- ITSM (6)
- MES (34)
- Řízení výroby (36)
- WMS (29)
- Dodavatelé IT služeb a řešení
- Datová centra (25)
- Dodavatelé CAD/CAM/PLM/BIM... (41)
- Dodavatelé CRM (38)
- Dodavatelé DW-BI (50)
- Dodavatelé ERP (68)
- Informační bezpečnost (50)
- IT řešení pro logistiku (45)
- IT řešení pro stavebnictví (26)
- Řešení pro veřejný a státní sektor (27)


















![]() | Přihlaste se k odběru zpravodaje SystemNEWS na LinkedIn, který každý týden přináší výběr článků z oblasti podnikové informatiky | |
![]() | ||
Co může kvalitní ERP přinést do výrobního podniku
Stejně jako v jiných průmyslových odvětvích tak i ve výrobě sílí potřeba podniků nalézt ideální nástroj pro plánování výroby, který umožní optimalizovat respektive zvýšit produkci. Cílem je dosažení maximalizace vytížení a optimalizace nákladů při dodržení termínu dodání. Toho lze dosáhnout pouze dodržováním stanovených postupů ve všech fázích plánování.


Při výběru a implementaci robustního ERP, který je pro výrobní sektor nutností, je třeba si uvědomit, že plánování výrobního procesu je ovlivňováno mnoha faktory. Zohlednění všech proměnných vstupujících do plánu je pro manuálního plánovače velmi složité a proto je nezbytné použít sofistikovaný ERP systém, který obsahuje integrované řešení pro řízení výroby, případně APS nástroj, který umožní optimalizaci výrobního i logistického procesu. Vysoká míra automatizace řady činností dává jen minimální prostor k chybovosti uživatelů a umožňuje maximální efektivitu při řízení výrobních společností.
Výběr ERP ve výrobním podniku
Na trhu je dostupná celá řada ERP systémů nebo samostatných řešení pro výrobu, ovšem jedním z klíčových faktorů výběru je volba správného oborového řešení a jeho přínos směrem k omezení počtu potřebných customizací. V případě nasazení kvalitního nadstavbového řešení jich nemusí být tolik, jako kdyby společnost nasadila standardní ERP řešení a vyvíjela každý požadavek samostatně. Oborové řešení je v podstatě balík ověřených customizací, který je replikovatelný, vychází ze zkušenosti implementátora z oboru a v důsledku šetří zákazníkovi náklady.
Druhým scénářem je nasazení ERP a jeho integrace s produktem třetí strany – v tomto případě APS nástrojem pro pokročilé plánování výroby, který poskytuje mnoho dodatečných funkčností a tím opět snižuje počet potřebných dodatečných zákaznických programových úprav standardního systému.
Prioritou je plánování
Efektivita výroby vychází z kvality a přesnosti jejího plánování. Základním prvkem plánování je stanovení cíle. Cílů plánování výroby může být několik a v průběhu sestavování plánů je potřeba zohlednit velké množství faktorů, které do výrobního procesu vstupují.
Základním stavebním kamenem úspěchu výrobního procesu je dodržování plánovaných termínů s ohledem na požadavky svých zákazníků. Toho lze dosáhnout pouze v případě jasné prioritizace zakázek a optimalizace jejich pořadí. Výrobní zakázky musí být logicky sdružovány do výrobních dávek, které musí být plánovány společně. V každé fázi je potřeba předpokládat, že do výrobního plánu mohou neočekávaně vstoupit mimořádné zakázky či odstávky. Za každých podmínek musí být splněn ukazatel maximální možné efektivity využití kapacit strojů, jejich obsluhy a použitých nástrojů. Současně musí být udržovány dostatečné zásoby materiálu potřebného k výrobě a zohledněny termíny jeho dodávek.
Dodržení plánu a správná definice úzkých míst ve výrobě
Je velmi důležité, aby celé plánování bylo centralizováno v jednom plánovacím centru nebo u jednoho plánovače. Při narušení původního plánu nebo za přítomnosti dodatečných vstupů může dojít k zásadní změně výstupu a plánovací centrum musí na základě dostupných informací kontrolovat dodržení pravidla minimálního zásahu. Týká se to především výroby, která bezprostředně souvisí s dalšími navazujícími činnostmi, jako je kooperace, expedice, přísun materiálu do výroby nebo plánování nákupu. Tyto činnosti omezují zejména obchodníky, kteří vyžadují flexibilní změny výroby. Pro zachování možnosti operativního zásahu do plánu jsou nezbytné předem dohodnuté podmínky přicházejících změn. Velmi důležitá je komunikace mezi jednotlivými odděleními v prodejním a výrobním procesu. Jako nezbytnost se v tomto případě jeví sdílení informací v ERP systému.
V případě složitějších typů výroby – typicky výroba finálního produktu v několika fázích - je stanovení univerzálního klíče pro plánování výroby velmi složité. Výrobní operace se střídají a jednotlivá pracoviště jsou sdílena různými zakázkami. Takových zakázek může být mnoho současně a výrobní kapacity jsou omezené. V takové situaci je klíčové identifikovat úzká místa, přes které tyto zakázky prochází. Jedině pak je možné tato pracoviště dokonale vytížit stanovením pořadí průchodu zakázek. Okolo klíčového výrobního procesu se následně doplánují další výrobní operace. Pokud zmíněným pracovištěm prochází zakázka vícekrát, je optimalizace a numerické zpracování podstatně složitější. Je nutné do plánu doplňovat priority, podle kterých se zakázky na pracovišti řadí. Většinou se jedná o zakázky, které mají dlouhé technologické časy a operace na sebe nemusí bezprostředně navazovat.
Výše zmíněné nestandartní situace a komplikace mohou ve výrobním procesu nastat kdykoli a je jasné, že bez přítomnosti sofistikovaného ERP integrovaného s pokročilým plánovacím nástroje mohou způsobit výrobnímu podniku nemalé ztráty.
Pokročilé plánování kapacit a materiálu = APS
Jak již bylo řečeno, APS systémy mohou být integrální součástí ERP nebo je lze implementovat jako doplňkový software. Díky pokročilým analytickým a optimalizačním funkčnostem vytváří tyto systémy sofistikovaný mechanismus pro plánování a rozhodování ve výrobě.
APS systémy představují technologie, které se zabývají analýzou a plánováním výroby pro krátký, střednědobý i dlouhodobý horizont. Využívají pokročilé matematické algoritmy a obsahují logiku provádění optimalizace nebo simulace za účelem konečného naplánování kapacit a zdrojů. Umožňují reálně zvýšit dostupnou kapacitu výroby, zkrátit průběžné doby výroby a lépe garantovat přislíbené dodací termíny. Současně je systémem zohledňována řada omezení a obchodních pravidel v procesu plánování. APS často vytváří a vyhodnocuje několik scénářů a díky tomu je plánovací centrum nebo plánovač schopen efektivně využít své kapacity a splnit závazky udávané výrobními zakázkami.
Základní moduly většiny ERP systémů pro plánování podnikových zdrojů a realizaci výrobních procesů zřídka poskytují dostatečné nástroje pro efektivní řízení, dostatečnou simulaci a optimalizaci komplexních dodavatelských a výrobních řetězců. S použitím těchto základních řešení narůstá riziko neefektivity výroby způsobené např. silnými vazbami řízení procesů k jediné osobě nebo nedostatečnou kompatibilitou a dynamičností výrobních procesů.
APS na základě výpočtů v reálném čase, řeší tyto nedostatky v plánování podnikových zdrojů a umožňuje bezproblémovou integraci s ERP systémem, které klient používá. Díky širokému využití simulace poskytuje APS transparentní přehled o nejziskovějších výrobních scénářích. Kromě toho systém uvažuje různé indikátory plánování, pravidla a omezení a automaticky identifikuje možný nedostatek materiálu a zdrojů.
Vedle „čištění“ vlastních dat může být APS systém užitečný také v rámci interních procesů. Správná implementace a využití funkčností APS automaticky vyvolá nutnost ujasnění pravomocí a zodpovědností, změní styl řízení a delegování a donutí plánovací centrum zaměřit se na klíčové faktory, které výrobní proces ovlivňují.
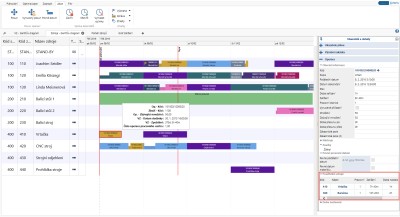
Ganttův diagram zdrojů na výrobních zakázkách
Pokročilé nástroje pro plánování mohou do tvorby a plnění výrobního plánu přinést řadu přidaných hodnot:
- Plánování do omezených kapacit
- Optimalizaci rozložení zátěže pomocí seznamu disponibilních pracovních nebo strojních center.
- Optimalizaci seřizovacích časů a výrobních dávek založené na opakovaném nastavení parametrů.
- Seskupování výrobních zakázek.
- Synchronizované plánování všech zainteresovaných zdrojů s respektováním všech známých omezení. Prostřednictvím propojení paralelních operací mohou být v ERP systému definovány výchozí podmínky a APS nástroj automaticky nalezne optimální variantu řešení.
- Grafické a interaktivní plánování. Změny v plánu se mezi ERP a APS oboustranně synchronizují v reálném čase. To zaručuje dodržení plánu v souladu s nastavením výrobních omezení.
- Vizuální ukazatele jako Ganttův diagram pro zdroje, grafy výrobních zakázek a zákazníků nebo graf zatížení či zobrazení pořadí zdrojů.
- Detailní analýzy plánování, které zobrazují vytížení při omezených nebo neomezených kapacitách pro identifikaci úzkých míst ve výrobě.
- Zohlednění dostupnosti vstupního materiálu - pomocí integrace plánovací metody MRP.
- Simulaci přímo ve výrobním plánu - uživatel v reálném čase obdrží odpovědi na otázky týkající se potenciálních změn na již rozpracovaných závazných zakázkách.
- Klíčové ukazatele výkonnosti a analýzu plnění dodacích termínů/zpoždění.
Shrnutí
Za přítomnosti výše uvedených technologických řešení je ideálním výstupem plánovacího procesu bezproblémové zkombinování všech dílčích cílů – maximální vytížení strojních kapacit, momentální dostupnost potřebného materiálu, minimalizace výrobních nákladů a dodání přijatých zakázek v očekávaném. Implementace pokročilého plánovacího nástroje může přinést výrobnímu podniku kontinuální růst efektivity všech výrobních procesů.
![]() |
Ing. Kateřina Tillingerová Autor článku je manažerkou marketingu společnosti NAVISYS, s. r. o. |


Formulář pro přidání akce