- Přehledy IS
- APS (20)
- BPM - procesní řízení (23)
- Cloud computing (IaaS) (10)
- Cloud computing (SaaS) (32)
- CRM (52)
- DMS/ECM - správa dokumentů (20)
- EAM (17)
- Ekonomické systémy (68)
- ERP (76)
- HRM (28)
- ITSM (6)
- MES (34)
- Řízení výroby (36)
- WMS (29)
- Dodavatelé IT služeb a řešení
- Datová centra (25)
- Dodavatelé CAD/CAM/PLM/BIM... (41)
- Dodavatelé CRM (38)
- Dodavatelé DW-BI (50)
- Dodavatelé ERP (68)
- Informační bezpečnost (50)
- IT řešení pro logistiku (45)
- IT řešení pro stavebnictví (26)
- Řešení pro veřejný a státní sektor (27)


















![]() | Přihlaste se k odběru zpravodaje SystemNEWS na LinkedIn, který každý týden přináší výběr článků z oblasti podnikové informatiky | |
![]() | ||
Změny v plánování výroby po nasazení APS systému
Zavedení APS systému, tedy systému pro pokročilé plánování, zásadně mění způsob plánování. Článek popisuje konkrétní zkušenosti, které byly získány při projektech zaměřených na implementaci japonského APS systému a při vytváření plánovacích prototypů u řady výrobních společností.


Při standardním plánování – z našich zkušeností se jedná u většiny podniků o plánování v Excelu – je hlavní a velmi cenné know-how v hlavě plánovače. Je to pro firmu velmi cenný člověk, ale plýtvá většinu svého času prováděním rutinní činnosti. APS systém přebírá rutinní práci a uvolňuje plánovači čas k činnostem, které může zvládnout jen člověk. Pokud si nejste jisti, zda APS může být ve vašem případě přínosem, položte si několik otázek týkajících se současného způsobu plánování:
- Je možné při současném systému plánování vytvořit dostatečně přesnou frontu práce pro všechna důležitá pracoviště? Odpověď zní „ne“, pokud výroba musí provádět další, podrobnější plánování. Například pokud se mistr nemůže spolehnout na plán a musí určovat pořadí dávek tak, aby byly správně zásobovány další procesy.
- Je fronta práce proveditelná? To znamená: bere plánovač v úvahu všechna omezení (materiál, nástroje, obsluhy, seřizovače)?
- Je možná simulace počtu obsluh a směnnosti na období několika týdnů?
- Je možná optimalizace pořadí dávek? (např. minimalizace časů nastavení, pořadí dávek podle barev)
Pokud odpověď na některé z otázek zní „ne“, je úvaha o APS systému na místě. Popíši, jaké změny můžete od nasazení plánovacího systému očekávat.
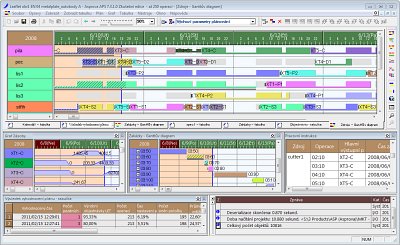
Standardní zobrazení plánu výroby - Gantův diagram
První velká změna nastává v oblasti získání dat pro plánování
Cesta dat do plánovacího Excelu je často dost složitá. Při nasazení APS se tato cesta napřimuje a částečně automatizuje. Interface zajišťuje, že plánovač má na jednom místě jak výrobní data, tak data dynamická – data o zásobách, požadavcích zákazníka, odpisech výroby a další. Po implementaci APS systému ve firmě KYB jsme se dotazovali manažera logistiky na přínosy. Na prvním místě uvedl: „Plánovač může konečně plánovat, nemusí se zabývat kopírováním a úpravami dat“. Možnost kontroly, a to že se data skutečně používají, způsobuje, že vyplavou na povrch chyby, které byly do té doby tolerovány (například chybně zpracovávané EDI zprávy, neuzavírané dodací listy, nepřesnosti ve výrobních datech atd.). Data se tak postupně zpřesňují, a tím se zlepšuje nejen plánování, ale i ostatní procesy. Plánovač může věnovat čas, který dříve trávil kopírováním a úpravami dat, tomu, aby se data zlepšovala už u zdroje.
Druhá zásadní změna nastává v samotném procesu plánování
Vytvoření plánu se redukuje na jedno kliknutí. Plán je pak vytvořen během několika desítek sekund. Není to samozřejmě tak úplně snadné – předem musí být sestaven plánovacího algoritmus, který přesně reflektuje požadavky na konkrétní výrobu. Pak se vytvořený plán blíží dokonalosti. Co takové vytvoření algoritmu znamená? I ve zdánlivě jednoduchých diskrétních výrobách je přesné nastavení plánovacího algoritmu poměrně složité. Je to způsobeno řadou omezujících požadavků na plán.
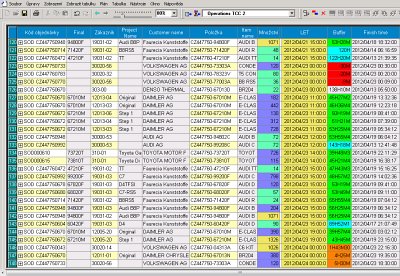
Přehled plnění objednávek
Typickou omezující podmínkou je velmi nízká meziprocesní zásoba. Představte si situaci, kdy existuje několik paralelních pracovišť s poměrně dlouhým časem nastavení (a tím požadavkem na kumulaci dávek). Ty zásobují následující proces (pec) s kontinuálním zpracováním. Jedná se o dva asynchronní procesy, ale meziprocesní zásoba na dopravníku před pecí může být maximálně jedna hodina. Spolu s požadavkem na optimalizaci počtu obsluh se jedná o poměrně složitou plánovací úlohu. Návrh ideálního algoritmu se v takových případech nemusí povést napoprvé. Je třeba postupovat iteračně – to znamená provést nastavení, algoritmus otestovat na konkrétních datech, provést úpravy a tento postup několikrát opakovat. Jen díky tomu, že APS systém umožňuje nastavování plánovacího algoritmu z připravených komponent, jsme schopni vyhovující plánovací algoritmy rychle navrhnout a zprovoznit. Programování takového plánovacího algoritmu na míru by trvalo týdny, s použitím stavebnicového systému je to otázkou hodin.
Třetí zásadní odlišností od plánování v Excelu je možnost snadno a přesně plánovat s více omezeními
Plán je tak skutečně „proveditelný“ a výroba nemusí provádět operativní změny způsobené nedostupností materiálu, obsluh, seřizovačů nebo přípravků. Podle požadavků konkrétní výroby je nastaveno, která z omezení jsou „tvrdá“ (to je typicky kapacita stroje) a která měkká (to mohou být třeba obsluhy nebo dostupnost materiálu). Pokud je např. obsluha nastavena jako měkké omezení, systém počítá potřebný počet obsluh a upozorňuje, kdy a o kolik bude překročen standardní počet. Ve srovnání s plánováním v Excelu se tak odstraní ztráty ve výrobě způsobené operativními změnami plánu. Hlavním požadavkem na plán bývá dodržení dodacích termínů. To znamená hlavně kontrolu časové rezervy mezi dokončením výroby a expedicí.
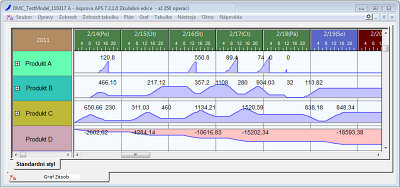
Graf úrovně zásob pro jednotlivé zdroje
Na rozdíl od plánování v Excelu je v APS systému snadné plánovat a řídit velikost bufferů hotových výrobků a polotovarů, a to i na období několika týdnů. Systém zajišťuje, aby buffer byl rovnoměrný u všech položek. Tím se vyhneme situaci, kdy u jedné položky je 200 % požadované bezpečnostní zásoby a u druhé jen 20 %. To umožňuje při stejné hodnotě zásob vázaných v bufferu hotových výrobků daleko větší jistotu včasné dodávky. Zároveň se snižuje riziko operativních změn ve výrobě, způsobených zjištěním „musíme expedovat, ale nemáme co“. Pokud se buffer v plánovaném období (typicky několik týdnů) pohybuje mimo požadované rozmezí (ať směrem nahoru nebo dolů) je možné rychle a snadno nasimulovat možná řešení, například úpravy směnnosti. Problém se odhaluje a řeší s daleko větším předstihem než při standardním plánování. To samé platí pro zásobu polotovarů. Uvedené změny umožní plánovači, aby za stejného úsilí vytvářel kvalitnější plán na delší období. Tím se může dosáhnout lepší efektivity výroby a nemalých finančních přínosů
Zdeněk Kurz
Autor působí jako vedoucí divize Asprova ve společnosti Aimtec.


Formulář pro přidání akce