- Přehledy IS
- APS (20)
- BPM - procesní řízení (23)
- Cloud computing (IaaS) (10)
- Cloud computing (SaaS) (31)
- CRM (52)
- DMS/ECM - správa dokumentů (20)
- EAM (17)
- Ekonomické systémy (68)
- ERP (75)
- HRM (28)
- ITSM (6)
- MES (33)
- Řízení výroby (36)
- WMS (28)
- Dodavatelé IT služeb a řešení
- Datová centra (25)
- Dodavatelé CAD/CAM/PLM/BIM... (41)
- Dodavatelé CRM (38)
- Dodavatelé DW-BI (50)
- Dodavatelé ERP (66)
- Informační bezpečnost (48)
- IT řešení pro logistiku (45)
- IT řešení pro stavebnictví (26)
- Řešení pro veřejný a státní sektor (27)


















![]() | Přihlaste se k odběru zpravodaje SystemNEWS na LinkedIn, který každý týden přináší výběr článků z oblasti podnikové informatiky | |
![]() | ||
Kanban – výroba tahem
Výhodou kanbanu a z něj odvozených systémů je schopnost snížit surovinové zásoby. Je samozřejmé, že jimi nelze řídit všechny komponenty, nicméně velmi se osvědčily v případě těch položek, které se používají opakovaně. V následujícím textu si představíme historii dílenského řízení kanban, jeho rozdělení, důvody, které vysvětlují, proč je výhodné jej zavést, a vše, co je s ním spojené. Systém kanban také zasadíme do celkového konceptu zlepšovacích metod štíhlé výroby a představíme si i související a nutné principy potřebné pro jeho aplikaci.


Začněme obecněji, a to přechodem z tlakového principu výroby na princip tahový. Tlakový princip je typický pro plánované hospodářství, kdy podniky vyrábí dle stanoveného plánu a odbyt je prakticky zajištěn díky nedostatku zboží. Tlakový princip je zachycen na obrázku 1. Podnik vyrábí určitý výrobek, který je trhem vcelku přijímán. Protože je trvalý nedostatek zboží na trhu, nemusí se podnik příliš starat o potřeby zákazníka, své výrobky k němu prostě dotlačí. Tento princip může fungovat i v tržním hospodářství, pokud na trhu není vysoký převis nabídky a výrobce má dostatečnou prestiž. V dnešní době stále ještě funguje tento princip poměrně intenzivně u módního zboží.
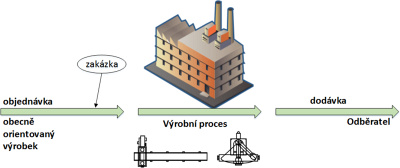
Obr. 1: Systém tlaku
Pokud je převis nabídky vysoký, zákazník si logicky více vybírá. Výrobce mu vychází vstříc tím, že nabízí v katalogu řadu možností, jak by si mohl zákazník svůj výrobek sestavit. V nejvyšší formě výrobce umožní zákazníkovi, aby si sám formou počítačového dialogu vytvořil z velkého množství předpřipravených modulů, dílců, příslušenství a barevných kreací svůj vlastní model a vytáhl si ho z výrobní linky (viz obrázek 2).
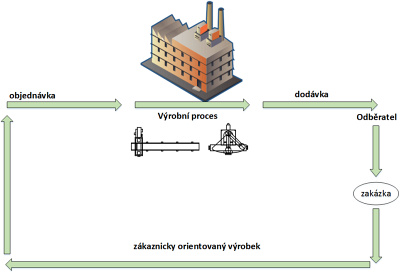
Obr. 2: Systém tahu
Kanban rovná se tah
Systém kanban je jedním ze základních představitelů tahového principu. Slouží jako nástroj jemného vyladění výroby i propojení jednotlivých procesů. Taichi Ohno jej zavedl ve výrobním závodu Toyoty již v roce 1953 s cílem optimalizovat zásoby při opakované sériové výrobě. Za zmínku ještě stojí, že fungování Kanbanu a JIT je založeno na téměř stejném principu. Tyto dva systémy bývají u některých autorů (např. Lambert) zaměňovány.
Název pochází z japonského slova kan (karta) a ban (signál). Jedná se o japonský systém dílenského řízení výroby. Podstata koncepce kanbanu je založená na poskytnutí pouze těch komponent ze strany dodavatele, skladu nebo výroby, které jsou zapotřebí, v daném množství a v daném čase tak, aby neexistovaly žádné přebytečné inventáře. Princip kanbanu vychází z předpokladu, že je možné rozdělit pracoviště na prodavače a kupující, přičemž je současně přesně definován okruh pracovišť, která si dodávají a odebírají materiál. O tom, jaké části budou jednotlivá pracoviště potřebovat, informují štítky (kanban), které cirkulují v rámci jednotlivých dílen.
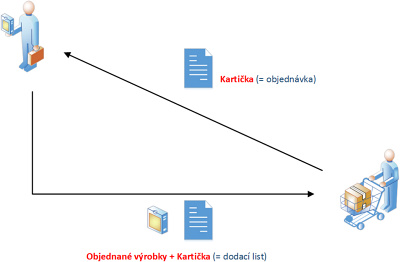
Obr. 3: Princip kanbanu
Ukažme si na příkladu supermarketu v základních osmi bodech princip Ohnem navržené, a časem stále zdokonalované metody:
- Zákazník si z regálu vezme požadované zboží.
- Na pokladně jsou ze zboží sejmuty kanbanové karty a položeny do skříňky (pošta kanban).
- Karty jsou poslány do skladu.
- Když je poté ze skladu odebráno zboží, které je potřeba pro naplnění regálů, jsou karty opět umístěny na konkrétním zboží, které identifikují.
- Zboží je nyní odvezeno do supermarketu a s kartami postaveno do regálů.
- Zboží je připraveno k prodeji, čímž se cyklus uzavře.
Předpokladem aplikace tohoto systému je několik skutečností. Každé pracoviště podniku musí vykonávat určitý soubor činností a vystupovat ve vztahu k ostatním pracovištím v roli vnitropodnikového zákazníka a dodavatele. Mezi další předpoklady patří, že všechny činnosti jsou vykonávány s vysokou jakostí, že odběratelská pracoviště odebírají od dodavatelských pracovišť pouze ten počet dílů, který potřebují ke splnění požadavku svého odběratelského pracoviště, a že požadavky jednotlivých pracovišť a jejich pozdější splnění jsou vyjadřovány formou štítku.
Druhy kanbanu
Kanban jako takový je určen především pro regulaci množství materiálu (vstupního materiálu, polotovarů, rozpracované výroby či hotových výrobků) ve výrobě. Jedná se tedy ve své podstatě o způsob zásobování pracovišť ve výrobním podniku. Dodavatelský kanban, tedy zásobování mezi více podnikatelskými subjekty, není tak častý a je efektivně nahrazován odvozenou metodou JIT. Další způsob dělení kanbanu vychází z použití či nepoužití papírové kartičky
Bezkartičkový kanban
Příkladem realizace může být dále uvedená případová studie aplikace systému tahu bez kanbanových karet. Pracoviště „sklad“ vyskladňuje polotovar, který se následně svařuje na pracovišti „svařování“ a na dalším pracovišti „vrtání“ se tento dílec vrtá. Část regálu na „svařovně“ byla tedy označena jako „VSTUP“ a bylo zde vyčleněno místo pro dva dílce. Jakmile „sklad“ vidí, že na „svařovně“ chybí v regálu polotovar, vyskladní ho a doplní do místa označeného jako VSTUP do regálu na „svařovně“. Jakmile je regál plný (jsou v něm dva dílce), další polotovar se pro „svařovnu“ nedodává a vyskladňuje se pro jiná pracoviště (např. „montáž“). Ve chvíli, kdy pracovník na „svařovně“ odebere z regálu polotovar na opracování, vidí jedno volné místo a po vyskladnění pro „montáž“ začne opět vyskladňovat polotovary pro „svařovnu“. Stejným principem zásobuje „svařovna“ následující pracoviště „vrtání“. To znamená, že když je v regálu „vrtání“ plno, nevyrábí pracoviště „svařování“ další dílce pro „vrtání“. To vede k tomu, že ani „sklad“ nevyskladňuje polotovary pro „svařování“. Když ovšem pracovník „vrtání“ odebere kus z regálu „VSTUP“, začne pro něj vyrábět „svařovna“ další dílec a tím vezme jeden polotovar ze svého vstupního regálu, což je signál pro „sklad“, že může dodat další polotovar pro „svařování“. Tím je zajištěno, že mezi pracovišti je řízena zásoba rozpracovaného materiálu.
Takto bylo propojeno několik pracovišť a vznikl systém tahu na základě signálu. Signálem je zde neobsazené místo regálu, které musí být dostatečně viditelné, pokud plánovaný maximální počet dílců čekajících na zpracování na daném pracovišti není zcela naplněn.
Identifikace kanbanu kanbanovou kartou
Princip spočívá v tom, že dílce jsou uskladněny do regálů či kontejnerů v přesně definovaném počtu kusů zajišťujícím zásobu na určený čas chodu výroby. Každý kus (položka) je identifikován kanbanovou kartou. Ve chvíli, kdy je odebrána položka zásoby, je z ní současně odebrána kanbanová karta a je pověšena na kanbanovou tabuli příslušného pracoviště. Dodavatelská pracoviště si v přesně stanovených časových intervalech z tabule kartu vyzvednou a na jejím základě zahájí dodávku požadované položky. Bez této karty nesmí bez ohledu na aktuální stav plánu dispečer zahájit dodávku na danou položku. Jakmile je odebrána další položka ze zásoby, je opět sejmuta kanbanová karta a umístěna do kanbanové tabule s tím, že dodávka požadované položky probíhá stejně jako ve výše uvedeném případě. Tento proces se neustále opakuje.
V současné době je v mnoha případech systém Kanban řízen pouze elektronicky, kdy nekoluje žádná karta, ale vše se řeší pomocí čtečky čárových nebo QR kódů. Ve chvíli, kdy je odebrána položka zásoby, se načte kód její specifikace a ihned poté se objeví požadavek po dané položce na dodavatelském pracovišti.
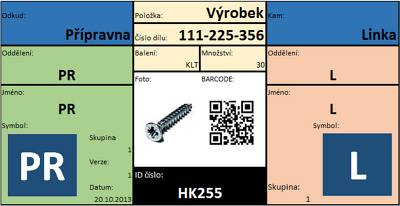
Obr. 4: Obsah kanbanové karty – bar kód, název dílu, číslo dílu (P.N.), typ balení, množství kusů v balení, fotografie dílu, odpisové středisko (důležité pro správné odepisování materiálu), cílová adresa (přesnější popis místa, kam má být přepravka uložena), kanban číslo
Důvody pro zavedení systému
Výpočet ekonomické návratnosti projektu nebývá triviální. Ty položky, které přinášejí průběžné (každodenní) úspory nebo zvýšené výkony, musí ve své sumě pokrýt náklady na realizaci krizových scénářů, jejichž pravděpodobnost není vždy snadno stanovitelná (expresní opravy, náhradní materiálové vstupy apod.). Docházíme tak k úvaze o nutnosti jakýchsi „optimálních tělesných parametrů“ daného výrobního systému, tj. parametrů odpovídajících jeho dlouhodobě zabezpečenému ekonomickému zdraví. Kvalitativně vyjádřené důvody pro zavedení systému jsou:
- zavedením systému kanban dochází ke snižování velikosti výrobních dávek, čímž je možná pružnější reakce na potřeby zákazníka,
- menší výrobní dávka znamená méně dílů v oběhu, což snižuje požadavky na prostor a snižuje ztráty u nekvalitní výroby, roste produktivita,
- nižší požadavky na prostor a nižší ztráty z nekvalitní výroby znamenající úsporu financí,
- systém řízení kanban znamená posun od „tlačeného“ k „tahovému“ materiálovému toku, tj. vyrábí se, jen když existuje objednávka,
- systém řízení kanban napomáhá k výrobě JIT (just in time), tj. výrobě právě v čase, kdy to potřebujeme,
- tento systém je jednoduchým vizuálním systémem řízení. [1]
Dlouhodobě efektivní (tj. ekonomicky návratná) investice do projektu štíhlé výroby musí být zdůvodněna nejen prokázáním zlepšení parametrů typu okamžité produktivity, ale také tím, že potenciál tohoto zlepšení je schopen absorbovat důsledky zavedení štíhlosti, důsledky typu rizik.
Důvody pro zavedení systému kanban lze vyjádřit i kvantitativně. Matematická analýza aplikovaná pro účely optimalizace nás jednoznačně učí, že optimum libovolné kriteriální funkce je v prostoru vždy jejím extrémem (tj. minimum nebo maximum) vymezeným podmínkami platnosti této funkce. Je tedy třeba se ptát, co chceme pomocí konceptu štíhlé výroby (kanban jako takový ovlivňuje právě tento výsledek) minimalizovat, a co maximalizovat a zda extremalizace jednoho nebude působit nežádoucí extremalizaci druhého. Bude-li průtok (throughput) systému T vyjádřený jako rozdíl mezi hodnotou produktu (tj. prodejní cenou) a hodnotou nákladů produktu (tj. zejména výdajů na opatření vstupů pro jeho výrobu) a budeme-li přitom dosahovat provozních nákladů OE (operational expenses), pak celková produktivita systému bude rovna podílu T a OE. Jako přímý ukazatel štíhlosti se pak nabízí převrácená hodnota tohoto podílu (kladné relativní číslo, které je tím nižší, čím bude systém štíhlejší):
štíhlost výrobního systému = provozní náklady / průtok
neboli: lean production index LPI = OE / T
Dokud všechno půjde tak, jak má, bude tento ukazatel platit. Jinými slovy, LPI je krátkodobý, nebo dokonce jen okamžitý ukazatel štíhlosti. Dlouhodobé hledisko totiž nemůže pominout výše zmíněnou oblast rizik, která může proces „zeštíhlování“ nastolit. Krizové scénáře, které tato rizika pokrývají, jsou charakterizovány dvěma základními parametry. Prvním z nich je náklad na realizaci scénáře DE (distress expenses), druhým je pravděpodobnost uplatnění rizika DP (distress probability). Pro stanovení reálného (dlouhodobého) parametru štíhlosti je tedy třeba provozní náklady OE povýšit o sumu nákladů na pravděpodobné uplatnění nákladů na realizaci krizových scénářů za určité rozhodné období – sum [DE*DP]:
real lean production index RLPI = (OE + sum [DE*DP]) / T
Čeho bychom měli dosáhnout v procentuálním vyjádření a konkrétních parametrech, je uvedeno dále:
- snížení zásob ve výrobě o 60–90 %,
- redukce seřizovacích časů o cca 95 %,
- zkrácení průběžných časů výroby o 50–80 %,
- redukce potřeby ploch o cca 50 %,
- snížení personálních nákladů o cca 60 %,
- snížení nákladů na kvalitu o 20–60 %.“ [3]
Použitá literatura
- [1] Liker J. K. 2004. The Toyota Way – 14 Management Principles. New York: McGraw-Hill.
- [2] Ohno T. 2005. Toyota Production System: Beyond Large-Scale Production. New York: Productivity Press.
- [3] http://www.dynamicfuture.cz/kanban/
Michal Šimon, Antonín Miller
Ing. Antonín Miller je doktorandem na katedře průmyslového inženýrství a managementu Západočeské univerzity v Plzni. Ve své práci se zaměřuje na výrobní layout, digitální podnik a logistiku.


![]() ![]() | ||||||
Po | Út | St | Čt | Pá | So | Ne |
1 | 2 | 3 | 4 | 5 | 6 | |
7 | 8 | 9 | 10 | 11 | 12 | 13 |
14 | 15 | 16 | 17 | 18 | 19 | 20 |
21 | 22 | 23 | 24 | 25 | 26 | 27 |
28 | 29 | 30 | 31 | 1 | 2 | 3 |
4 | 5 | 6 | 7 | 8 | 9 | 10 |
11.7. | CyberEdu Letní škola |
23.9. | PragVue 2025 |
1.10. | Cyber Attacks 2025 |
21.10. | Bezpečnosť a dostupnosť dát 2025 |
11.11. | Umělá inteligence v IT infrastruktuře 2025 |
Formulář pro přidání akce
29.9. | The Massive IoT Conference |