- Přehledy IS
- APS (20)
- BPM - procesní řízení (23)
- Cloud computing (IaaS) (10)
- Cloud computing (SaaS) (32)
- CRM (52)
- DMS/ECM - správa dokumentů (20)
- EAM (17)
- Ekonomické systémy (68)
- ERP (76)
- HRM (28)
- ITSM (6)
- MES (34)
- Řízení výroby (36)
- WMS (29)
- Dodavatelé IT služeb a řešení
- Datová centra (25)
- Dodavatelé CAD/CAM/PLM/BIM... (41)
- Dodavatelé CRM (38)
- Dodavatelé DW-BI (50)
- Dodavatelé ERP (68)
- Informační bezpečnost (50)
- IT řešení pro logistiku (45)
- IT řešení pro stavebnictví (26)
- Řešení pro veřejný a státní sektor (27)
Partneři sekce
Tematické sekce


















Branžové sekce
![]() | Přihlaste se k odběru zpravodaje SystemNEWS na LinkedIn, který každý týden přináší výběr článků z oblasti podnikové informatiky | |
![]() | ||
Partneři webu
IT SYSTEMS 10/2007 , Plánování a řízení výroby , Plánování a řízení výroby
Když se řekne procesní výroba, leckomu vytane na mysli otázka, o jaké jde procesy, že se vymykají běžným konceptům plánování a řízení v ERP systémech? Nevím, jak se slovo „procesní“ dostalo do názvu označujícího námi myšlený typ výroby odlišný od výroby strojírenské. Patrně měl autor takového označení na mysli podmínky, při nichž se výrobní proces nejeví jako člověkem či strojem prováděná přeměna vstupů na složené celky, ale k přeměně dochází jaksi samovolně vlivem procesů řízených přírodními zákony. Tak vše, co probíhá v přírodě, má nádech chaosu a podléhá náhodným vlivům, s nimiž člověk moc nenadělá. Je v podobných podmínkách vůbec možné mluvit o efektivním řízení, když neexistují jasně vyčíslitelné údaje a normy, z nichž by bylo možné předpovídat budoucnost a průběh výrobního procesu ve formě dostatečně objektivního plánu výroby?
Po šesti letech mého působení v rámci vývojového týmu v podniku Synthesia Semtín na tvorbě systému plánování a řízení výroby barviv a pigmentů jsem měl možnost pochopit, nakolik jsou lidé z oboru chemické výroby zatíženi pochybnostmi, s nimiž považují každý ambiciózní projekt směřující k pevnému uchopení procesů v jejich branži za idealismus hraničící s nepochopením objektivní reality. Specifikem procesní výroby je její odpor k pevné struktuře a značná neurčitost, s níž lze těžko postihovat probíhající děj s očekávanou mírou přesnosti. Když se někde něco vaří, reaguje a mísí v obřím hrnci o objemu několika tun, vyvolává to velký respekt pozorovatele. Raději se držet v povzdálí, neboť kdo ví, co to udělá. Tak i samotní chemici a technologové vědí, že kusovník v jejich případě je pojem poněkud mlhavý a technologický postup sestávající s úkonů typu nasaď, zamíchej, ohřej, sleduj a dosypávej podle okamžitého stavu, jímž prochází klokotající masa v ocelové kádi, má nádech magických formulí. Není žádným velkým překvapením, když z očekávaného výrobku, pro který byly dodrženy všechny normy množství i kvality patřičné násady, se nakonec vyklubalo něco úplně jiného, nebo se vlivem atmosférických poruch látka beznadějně srazila v ohavnou a beztvarou hmotu, kterou bude nutné několik dní z kádě odsekávat majzlíkem a vyhodit do odpadu. Ale přejděme k poněkud sofistikovanějšímu pohledu na procesní výrobu a řekněme si alespoň základní fakta a pojmy, jimiž je možné ji charakterizovat.
Dávková výroba probíhá v šaržích, přičemž jednou šarží se rozumí množství látky, které lze vyrobit z jedné násady vstupních komponent v rámci jednoho kontinuálního cyklu. Toto množství je obvykle dáno kapacitou výrobní aparatury, resp. objemem konkrétních jejích prvků (kádí, pecí a p.), v nichž probíhá reakce či proces transformující celý objem počáteční směsi ve výsledný produkt. Výsledkem nemusí být jen produkt sám, ale mohou vznikat i vedlejší produkty, které nejsou pouhým odpadem, ale představují látku použitelnou pro další výrobu. Vlastní výrobní cyklus se potom může řetězit z počáteční fáze, při níž výrobek vzniká v surové podobě, s následnými operacemi, při nichž se surová látka přečerpává či jinak putuje k dalším výrobním zařízením za účelem její potřebné úpravy do požadovaného tvaru a konzistence.
Jak je vidět, naráží informační systém pro řízení procesní výroby na úskalí, která ve strojírenské výrobě nemají obdobu. Přesto existuje řešení, které se pokusím popsat s pomocí konkrétního příkladu použití dávkového modelu systému dynamického plánování a řízení výroby AROP. Příklad se týká reálného vzorku dat pro výrobu organické kyseliny s fiktivním názvem Abradabra. Vzorek dat připravila společnost Arsiqa system za účelem prezentace systému AROP pro Výzkumný ústav organických syntéz v Pardubicích (VUOS).
Obr. 1: Souhrnná THN norma spotřeby
Obr. 2: Struktura technické dokumentace
Obr. 3: Časový rozvrh výroby
Není v možnostech tohoto článku popsat detailně technologii virtuálního podniku v systému AROP. Pro nahlédnutí výhod metody MSO v systému dynamického plánování procesní výroby snad postačí, když řekneme, že znázorněný časový rozvrh výroby je výsledkem zcela automatických procesů počítačového zpracování vycházejícího z pouhého primárního požadavku obsluhy naplánovat výrobu tří tun kyseliny Abradabra. Navíc tento výpočet včetně simulace výroby celého výrobního podniku zahrnující všechny výrobky v několikaměsíčním plánovacím horizontu netrvá déle než několik minut.
Obr. 4: Graf vytížení souboru zařízení
Obrázek 5 znázorňuje postupné obsazování jednotlivých prvků souboru zařízení sestávajícího z částí aparatury A10 až A14 a filtrovacího zařízení tak, jak vyplývá z použitých cest daným souborem zařízení podle technologických parametrů výrobku z jeho reglementu. Z uvedené praktické ukázky je snad bez větších pochyb vidět, že i v procesní výrobě lze pracovat s pokročilým plánem výroby, podle kterého se dá vyrábět a řídit výrobu v omezených kapacitách. Doplňujícím argumentem pro toto tvrzení je skutečnost, že také v modelu procesní výroby je metoda MSO výrazem dynamického plánu, který je schopen v reálném čase automaticky reagovat na všechny události a změny, které mají dopad do časového rozvrhu výroby. Následné řízení výroby v systému AROP potom respektuje všechna výše uvedená specifika týkající se jak evidence skutečných spotřeb odlišných od norem spotřeby a řízení hmotného toku v závislosti na výsledcích všech kontrol jakosti, tak i evidence zásob ve struktuře sledovatelnosti a identifikace obalů v rámci celých konsignací pro jednotlivé jakostní dávky.
Obr. 5: Výrobní obsazenost prvků souboru zařízení
Autor je ředitelem společnosti Arsiqa system.
Jak plánovat procesní výrobu
Radim Lhoták
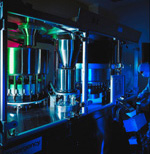


Po šesti letech mého působení v rámci vývojového týmu v podniku Synthesia Semtín na tvorbě systému plánování a řízení výroby barviv a pigmentů jsem měl možnost pochopit, nakolik jsou lidé z oboru chemické výroby zatíženi pochybnostmi, s nimiž považují každý ambiciózní projekt směřující k pevnému uchopení procesů v jejich branži za idealismus hraničící s nepochopením objektivní reality. Specifikem procesní výroby je její odpor k pevné struktuře a značná neurčitost, s níž lze těžko postihovat probíhající děj s očekávanou mírou přesnosti. Když se někde něco vaří, reaguje a mísí v obřím hrnci o objemu několika tun, vyvolává to velký respekt pozorovatele. Raději se držet v povzdálí, neboť kdo ví, co to udělá. Tak i samotní chemici a technologové vědí, že kusovník v jejich případě je pojem poněkud mlhavý a technologický postup sestávající s úkonů typu nasaď, zamíchej, ohřej, sleduj a dosypávej podle okamžitého stavu, jímž prochází klokotající masa v ocelové kádi, má nádech magických formulí. Není žádným velkým překvapením, když z očekávaného výrobku, pro který byly dodrženy všechny normy množství i kvality patřičné násady, se nakonec vyklubalo něco úplně jiného, nebo se vlivem atmosférických poruch látka beznadějně srazila v ohavnou a beztvarou hmotu, kterou bude nutné několik dní z kádě odsekávat majzlíkem a vyhodit do odpadu. Ale přejděme k poněkud sofistikovanějšímu pohledu na procesní výrobu a řekněme si alespoň základní fakta a pojmy, jimiž je možné ji charakterizovat.
Základní pojmy
Podle obecné představy laiků je chemická výroba kontinuální. Rozumí se tím fakt, že hmotný tok v ní neprobíhá po kusech a mezi jednotlivými výrobními kroky není možná časová prodleva. Přechod od jednoho prvku výrobního zařízení k druhému musí být nepřetržitý a výrobky na jednotlivých výrobních prostředcích nelze libovolně střídat. Jednotlivé kroky výrobního cyklu nelze navíc obvykle normovat a určit jednoznačně dobu jejich trvání. To je ovšem jen jedna část problému. Proces postupné přeměny surovin na hotový výrobek nemusí být kontinuální v celém svém průběhu. Ve skutečnosti se chemická výroba dělí na kontinuální a diskontinuální. První typ, jejímž reprezentantem jsou například rafinérie, ponechme stranou našeho zájmu a věnujme se druhému typu, kdy výrobek vzniká postupně z výrobních mezistupňů, tzv. polotovarů, tedy z výrobků nižší úrovně, které je možné i nutné skladovat a tvoří zásobu rozpracované výroby. Pro takový typ výroby se častěji používá termín dávková výroba.Dávková výroba probíhá v šaržích, přičemž jednou šarží se rozumí množství látky, které lze vyrobit z jedné násady vstupních komponent v rámci jednoho kontinuálního cyklu. Toto množství je obvykle dáno kapacitou výrobní aparatury, resp. objemem konkrétních jejích prvků (kádí, pecí a p.), v nichž probíhá reakce či proces transformující celý objem počáteční směsi ve výsledný produkt. Výsledkem nemusí být jen produkt sám, ale mohou vznikat i vedlejší produkty, které nejsou pouhým odpadem, ale představují látku použitelnou pro další výrobu. Vlastní výrobní cyklus se potom může řetězit z počáteční fáze, při níž výrobek vzniká v surové podobě, s následnými operacemi, při nichž se surová látka přečerpává či jinak putuje k dalším výrobním zařízením za účelem její potřebné úpravy do požadovaného tvaru a konzistence.
Plán a skutečnost
Další specialitou dávkové výroby je skutečnost, že nelze většinou plánovat výrobu pouze jedné šarže, byť by se mělo jednat o několik tun výrobku. Příprava celé aparatury pro takovou výrobu a její následné vyčištění může totiž znamenat několik dnů práce a výroba jedné šarže by se tak značně prodražila. Plánují se proto dlouhodobé sledy šarží, kterým se říká kampaně. Jedna kampaň chemického provozu představuje desítky až stovky tun rozdělených v dávkách následujících bezprostředně po sobě vždy na vyčleněné části výrobního systému tvořícího aparaturu. Výsledné produkty je dále nutné plnit do obalů či zásobníků, jejichž obsah musí být jednoznačně identifikovatelný z hlediska jeho kvality. Když se zmiňujeme o kvalitě, je třeba v této souvislosti říci, že jakost výrobků zde doslova předurčuje jejich následné použití. V případě sledování sytosti či obsahu aktivních látek v roztoku má význam i výtěžnost celého procesu a čisté množství stoprocentní látky v hotovém výrobku. Systém řízení kvality a zajištění potřebných laboratorních zkoušek je proto nepostradatelnou součástí řízení procesní výroby. Důsledkem výrobního procesu závislého na jakosti jednotlivých komponent je potom již logický požadavek sledovatelnosti všech zásob z hlediska původu a kvality, bez něhož si nelze smysluplnou procesní výrobu ani představit.Jak je vidět, naráží informační systém pro řízení procesní výroby na úskalí, která ve strojírenské výrobě nemají obdobu. Přesto existuje řešení, které se pokusím popsat s pomocí konkrétního příkladu použití dávkového modelu systému dynamického plánování a řízení výroby AROP. Příklad se týká reálného vzorku dat pro výrobu organické kyseliny s fiktivním názvem Abradabra. Vzorek dat připravila společnost Arsiqa system za účelem prezentace systému AROP pro Výzkumný ústav organických syntéz v Pardubicích (VUOS).
Způsob řešení
Systém AROP využívá metodu MSO (Modelování, Simulace, Optimalizace) jako základní koncept pokročilého plánování výroby do omezených kapacit. Simulací se zde rozumí virtuální napodobení výrobního procesu jako takového. V případě dávkového typu procesní výroby bylo proto nutné zahrnout do počítačového modelu reálného světa objektů všechny výše zmíněná specifika a entity tak, aby modelový proces odpovídal objektivní realitě. Proti strojírenské výrobě jde o rozdílné pojetí již ve fázi definice výrobkových struktur, technologie výroby a kapacitní struktury výrobního systému. Souhrnným názvem pro technickou dokumentaci výroby (TPV) je receptura, u složitějších provozů také reglement. Receptura zahrnuje THN normu spotřeby surovin a komponent výrobku a v zásadě se podobá klasickému kusovníku. Na obrázku 1 je zobrazen strukturní rozpad tříúrovňové skladby výrobku kyseliny Abradabra procházející postupnými stádii dvou polotovarů schopných jisté doby skladování. Proti standardnímu kusovníku jsou zde vidět pozice se záporným množstvím spotřeby. Ty vyjadřují vedlejší produkty, které při výrobě vyššího celku nejsou spotřebovány, ale naopak vznikají. Pokud se jedná o výrobky či látky použitelné v další výrobě, snižuje logicky jejich hodnota náklady na vstupní suroviny. Proto ono znaménko minus. Dalším typickým vstupem procesní výroby jsou technologické energie. Ty mají často výrazný podíl na nákladové ceně výrobku, proto je nutné je chápat jako jednicové spotřeby a podle toho je také normovat, i když v reálném procesu se nezaznamenává jejich skutečná spotřeba.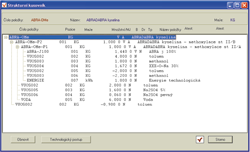
Obr. 1: Souhrnná THN norma spotřeby
Technologické vzory
Podstatnější rozdíl proti strojírenskému modelu výroby lze nalézt v technologické dokumentaci. Systém AROP definuje tři oblasti datových objektů popisujících technologické vzory procesní výroby:Výrobní předpis
Jde o sled technologických kroků seskupených do řetězců odpovídajících jednotlivým fázím výrobního cyklu. První fází je vždy výrobní operace, při níž vzniká surový produkt za kontinuálního průběhu všech úkonů technologického řetězce. Následující fáze probíhají v diskontinuálním režimu jako operace běžného technologického postupu a představují úpravy surového produktu jako sušení, filtrace a podobně. Tyto fáze v případě ryze kontinuálního cyklu výroby samozřejmě chybějí. Jednotlivé úkony neobsahují časové normativy, zato k nim lze přiřadit neomezený počet technických (procesních) parametrů, jimiž lze určovat podmínky, za nichž mají jednotlivé úkony probíhat. Jedná se například o stanovené teploty reakce, hustoty a podobně. Ty pak mohou být předmětem mezioperační kontroly.Technologické parametry
Každé fázi výrobního cyklu odpovídá jeden záznam technologických parametrů výroby. Ten určuje mimo jiné normativní časy potřebné na realizaci jedné výrobní fáze při výrobě jedné šarže od jejího zahájení k jejímu ukončení. Jedná se o celkovou dobu zpracování dávky, kterou lze obvykle snadno zjistit i stanovit. V rámci záznamu technologických parametrů výrobní operace je definována cesta výrobním zařízením. Přiřazuje výrobku všechny potřebné prvky ze souboru zařízení zajišťujícího celý kontinuální proces výroby. Takovým souborem mohou být dílčí části jedné či více aparatur, přičemž jejich výčet v rámci výrobní cesty výrobku může vyjadřovat úplnou či jen kritickou cestu z hlediska disponibilního využití konkrétních prvků souboru zařízení. Pokud se jedná o fáze následných úprav surového produktu, přiřazuje záznam technologických parametrů konkrétním úkonům skupinu zaměnitelných strojů podobně jako ve strojírenské výrobě (např. 5 sušiček).Výrobní zařízení
Zdrojem výrobní operace je soubor výrobních zařízení definující každý relevantní prvek složitých aparatur použitelných k vlastní výrobě. Ten se, jak ukazuje obrázek 2, může skládat z různých typů prostředků (kádě, čerpadla, filtry), přičemž každý typ má určený počet zaměnitelných představitelů. Součástí cesty výrobku výrobním zařízením je i definovaný počet použitých představitelů z tohoto disponibilního množství.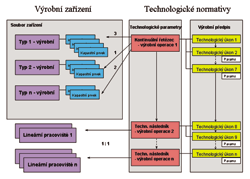
Obr. 2: Struktura technické dokumentace
Simulace výroby
Pro účely kapacitního plánování a rozvrhování výroby je možné v rámci technologické dokumentace definovat pro výrobek více variant cest, z nichž systém v průběhu simulace vybírá tu variantu, která je v daném simultánním časovém okamžiku otevřená, čili jejíž všechny prvky jsou neobsazené. Tím už se dostáváme k vlastnímu principu simulace výroby, jímž se provádí plánování kapacit a rozvrhování výroby v čase a prostoru celé výrobní organizace. Simulační model výrobního procesu v systému AROP si lze představit jako virtuální výrobní provoz, v němž dochází k realizaci výroby tak, jako by se jednalo o skutečný výrobní proces. Výsledky simulace výroby kyseliny Abradabra přes všechny tři výrobní stupně jsou vidět na obrázku 3. Každá úsečka grafu představuje dobu výroby jedné šarže o objemu pět set kilogramů z kampaně zahrnující plánované množství tři tuny hotového výrobku.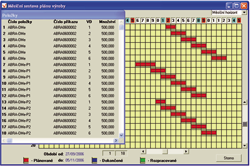
Obr. 3: Časový rozvrh výroby
Není v možnostech tohoto článku popsat detailně technologii virtuálního podniku v systému AROP. Pro nahlédnutí výhod metody MSO v systému dynamického plánování procesní výroby snad postačí, když řekneme, že znázorněný časový rozvrh výroby je výsledkem zcela automatických procesů počítačového zpracování vycházejícího z pouhého primárního požadavku obsluhy naplánovat výrobu tří tun kyseliny Abradabra. Navíc tento výpočet včetně simulace výroby celého výrobního podniku zahrnující všechny výrobky v několikaměsíčním plánovacím horizontu netrvá déle než několik minut.
Výstupy pro optimalizaci
Povšimněme si ještě způsobu, jakým lze nad okamžitým plánem výroby analyzovat využití a přidělení zdrojů v celém plánovacím horizontu za účelem jejich optimalizace. Na obrázku 4 je graf vytížení celého souboru zařízení využívaného k výrobě Abradabra kyseliny. Z něho je patrný kapacitní náběh jednotlivých kampaní v souběhu respektujícím nutné výrobní návaznosti polotovarů i jejich možný překryv.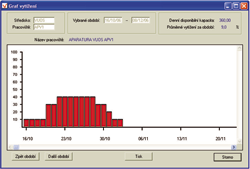
Obr. 4: Graf vytížení souboru zařízení
Obrázek 5 znázorňuje postupné obsazování jednotlivých prvků souboru zařízení sestávajícího z částí aparatury A10 až A14 a filtrovacího zařízení tak, jak vyplývá z použitých cest daným souborem zařízení podle technologických parametrů výrobku z jeho reglementu. Z uvedené praktické ukázky je snad bez větších pochyb vidět, že i v procesní výrobě lze pracovat s pokročilým plánem výroby, podle kterého se dá vyrábět a řídit výrobu v omezených kapacitách. Doplňujícím argumentem pro toto tvrzení je skutečnost, že také v modelu procesní výroby je metoda MSO výrazem dynamického plánu, který je schopen v reálném čase automaticky reagovat na všechny události a změny, které mají dopad do časového rozvrhu výroby. Následné řízení výroby v systému AROP potom respektuje všechna výše uvedená specifika týkající se jak evidence skutečných spotřeb odlišných od norem spotřeby a řízení hmotného toku v závislosti na výsledcích všech kontrol jakosti, tak i evidence zásob ve struktuře sledovatelnosti a identifikace obalů v rámci celých konsignací pro jednotlivé jakostní dávky.
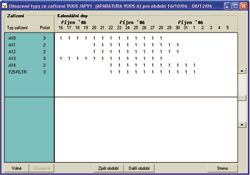
Obr. 5: Výrobní obsazenost prvků souboru zařízení
Závěr
V úvodu článku jsem mluvil o nedůvěře řídících pracovníků z chemické branže k exaktním metodám plánování a počítačového řízení procesní výroby. Dokumentuje to i naše zkušenost v podniku VUOS, pro který společnost Arsiqa system připravila uvedený vzorek. Ve výsledku nám nebylo ani umožněno prezentovat v tomto článku popsané výstupy před plénem vedení společnosti s odůvodněním, že námi navrhované metody a připravenost výroby na tak pokročilou inovaci systému řízení neodpovídají stávajícím poměrům ve výrobě. Je to myslím škoda pro obě strany.Autor je ředitelem společnosti Arsiqa system.
Chcete získat časopis IT Systems s tímto a mnoha dalšími články z oblasti informačních systémů a řízení podnikové informatiky? Objednejte si předplatné nebo konkrétní vydání časopisu IT Systems z našeho archivu.


IT Systems podporuje
Formulář pro přidání akce
Další vybrané akce