- Přehledy IS
- APS (20)
- BPM - procesní řízení (23)
- Cloud computing (IaaS) (10)
- Cloud computing (SaaS) (32)
- CRM (52)
- DMS/ECM - správa dokumentů (20)
- EAM (17)
- Ekonomické systémy (68)
- ERP (75)
- HRM (28)
- ITSM (6)
- MES (34)
- Řízení výroby (36)
- WMS (29)
- Dodavatelé IT služeb a řešení
- Datová centra (25)
- Dodavatelé CAD/CAM/PLM/BIM... (41)
- Dodavatelé CRM (38)
- Dodavatelé DW-BI (50)
- Dodavatelé ERP (68)
- Informační bezpečnost (49)
- IT řešení pro logistiku (45)
- IT řešení pro stavebnictví (26)
- Řešení pro veřejný a státní sektor (27)


















![]() | Přihlaste se k odběru zpravodaje SystemNEWS na LinkedIn, který každý týden přináší výběr článků z oblasti podnikové informatiky | |
![]() | ||
Optimalizace logistických procesů v kontextu štíhlé výroby
Štíhlá výroba rozlišuje čtyři stavy, ve kterých se materiál a následně polotovar či rozpracovaná výroba mohou nacházet – výroba (technologický proces, kdy dochází k transformaci materiálu), skladování, manipulace – doprava a kontrola. Ovšem pouze při realizaci technologického procesu je materiálu přidávána hodnota, za kterou je zákazník ochoten zaplatit. Ostatní tři stavy pouze zvyšují náklady společnosti, a proto je cílem všech podnikatelských subjektů realizované procesy v rámci uvedených stavů minimalizovat, až úplně eliminovat.


Pro zjednodušení budu v článku používat spojení optimalizace logistických procesů, které pochopitelně není přesné. Optimum totiž představuje stav nejlepšího nastavení všech parametrů a jakákoli změna v nastavení by tento stav mohla jenom zhoršit. Dosáhnout v logistice optima je proto krásný, nicméně v praxi řízení podniku nereálný cíl. Mohli bychom tedy hovořit o zlepšování či zefektivňování logistických procesů, nicméně pojem optimalizace je v slangu praxe standardním pojmem, a proto se jej budeme držet.
Logistický proces je již pojem známý a každý z nás si pod ním představí procesy spojené s manipulací, transportem, skladováním a s tím vším spojenou i administrativní evidenci. Přesto není dlouho pryč doba, kdy si pod pojmem logistiky mnoho lidí představilo pouze převoz materiálu z místa na místo.
Podle Evropské logistické asociace logistika znamená: „Organizace, plánování, řízení a výkon toků zboží vývojem a nákupem počínaje, výrobou a distribucí podle objednávky finálního zákazníka konče tak, aby byly splněny všechny požadavky trhu při minimálních nákladech a minimálních kapitálových výdajích.“
V souhrnném měřítku můžeme konstatovat, že je pojem logistiky a logistických procesů již chápán všeobecně dobře, a to i v případech, že je v určitých podnikatelských subjektech tak nenazýváme a jsou schovány v jiných odděleních. Na druhou stranu si ovšem pouze málo prozíravých manažerů uvědomuje vliv logistických procesů na funkčnost výrobního systému a ještě menší množství si dokáže dobře spočítat, co realizace logistických procesů představuje za náklady.
Podle jednoho z nejlepších inovátorů a odborníků na řízení výroby a logistiky, pana Jana Košturiaka, zaměstnává oblast logistiky až 25 % pracovníků, zabírá 55 % ploch a čas, který stráví materiál v podniku, činní až 87 %. Náklady na logistiku se pak různí v daných podnicích a činí jednu z největších položek celkových nákladů na výrobek.
Tyto skutečnosti ukazují, jak velký vliv má logistika na výkonnost podniku, náklady podniku a jak ovlivňuje jeho konkurenceschopnost. Proto by se společnosti při budování svého štíhlého podniku měly zaměřit nejen na štíhlou výrobu, ale i štíhlou logistiku. V logistice se jedná například o tyto formy plýtvání, které je nutné odstranit:
- Zbytečné pohyby a manipulace výrobků a materiálu - je dodáváno příliš mnoho nebo příliš málo; zbytečná překládka, přesuny zásob, lidí a materiálu. Standardně se uvádí a ve většině našich studií to bylo potvrzeno, že na jednu technologickou operaci je až deset dalších činností. Myslíte, že to není možné? Tak počítejme – vyskladnění, odepsání materiálu v systému, naložení na transportní vozík, převoz, složení z vozíku ve výrobě, příjem materiálu v systému, skladování na pracovišti, manipulace z přepravky na stroj, manipulace ze stroje do přepravky, skladování v přepravce, transport na další pracoviště a možná odepsání operace v systému. To jsme v návaznosti na druhou technologickou operaci na dvanácti činnostech.
- Nadbytečné dokumenty a administrativa – přílišná dokumentace související s logistickými činnostmi, ruční evidence položek, vyplňování příliš druhů dokumentů, nadbytečná evidence.
- Špatné dokumenty v logistice - chybně vyplněné dokumenty, neúplná specifikace, chyby v kusovníku a následné chyby v informačním systému vlivem odpisování hotové výroby, špatné převody množství materiálu.
- Hledání materiálu a polotovarů – materiál není tam, kde ukazuje systém, systém ukazuje určitý počet položek a ve skladu žádný materiál není a naopak, systém materiál nemá, a tak ho automaticky objednává, a přitom je ho fyzicky ve skladu dostatek. Za každou z těchto situací následuje plýtvání časem řady lidí, kteří hledají rozdíly v počtu položek a srovnávají systém s realitou.
- Čekání – čekání na nakládku, čekání na vykládku; čekání na dovoz materiálu; čekání na kompletaci zásilky, čekání na uvolnění materiálu kvalitou či složení materiálu.
- Chyby v logistických činnostech - chybně naložená zásilka, nekompletní dodávka materiálu, inventarizační rozdíly ve skladech, pozdní dodávka materiálu či polotovarů.
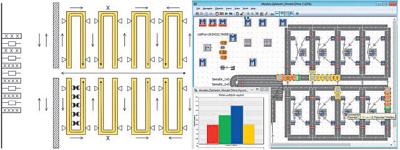
Je evidentní, že lze nalézt řadu problémů v nákupní, výrobní i distribuční logistice, a podle přístupu společností k řešení těchto problémů rozlišujeme dva stavy. Stav první je, že společnost si uvědomuje, že její logistické procesy jsou problémové (neefektivní) a snaží se s nimi pracovat, i když v mnoha případech ještě přesně neví jak. Druhý stav je, že mnoho společností vykonává své logistické procesy jako procesy, které jsou potřebné, ale s kterými nelze nic dělat, a tak je provádí tak jak jsou, bez jakéhokoliv sledu a rozmyslu. Nezajímá se tedy o to, zda by i tyto procesy šly zkrátit, zefektivnit a snížit náklady na ně vynakládané.
My bychom si měli vzít příklad z výrobních procesů, které jsou v drtivé většině případů již řádně zmapovány, zapsány a standardizovány v technologickém či montážním postupu a neustále dochází k jejich zlepšování. V logistických procesech tomu tak bohužel není, a proto bychom se měli zaměřit především na dvě oblasti:
- Standardizace logistických procesů – zajistit, aby se logistické procesy realizovaly vždy stejně bez ohledu na to, kdo a kdy je realizuje. Setkali jsme se s například s tím, že proces vyskladnění návěsu, evidence materiálu a následné zaskladnění do skladu byl v rámci ranní, odpolední a noční směny realizován třemi různými způsoby.
- Rovnoměrnost logistických procesů – jedná se o druhou problémovou oblast, kdy spíše než o rovnoměrnosti bychom měli hovořit o nerovnoměrnosti logistických procesů. Představme si, že na vyskladnění návěsu potřebuje jeden skladník třicet minut a v průběhu jedné směny má za úkol vyskladnit čtrnáct návěsů. Kolik tedy potřebuji skladníků? Podle normy stačí jeden skladník, protože čtrnáct návěsů dokáže vyskladnit za sedm hodin práce. To ovšem předpokládá, že přijíždí návěsy v průběhu směny vždy po 30 minutách a musíme tedy mít přesně definovaná a dodržovaná časová okna. Pokud bychom je definovaná neměli, může se sjet všech čtrnáct návěsů u příjmové zóny v 11 hodin a to již jeden skladník rozhodně stačit nebude, čímž nám stoupnou náklady na skladníky minimálně o jeden celoroční plat.
Aplikace metody milk run
Podívejme se nyní na další logistické úlohy, jejich problémy a potenciální možnosti řešení. Jednou ze složitějších úloh může být nastavení zavážení pracovišť s využitím metody milk run. K tomu se využívá dnes velmi populárního elektrického tahače se soupravou vozíků, přičemž v provozu výrobního systému může takových souprav být provozováno několik. Záleží na objemu a charakteru výroby i požadavcích na zásobování a nesmí se zapomenout, že pro efektivní aplikaci metody milk run je zapotřebí výrobu synchronizovat. Tím se dosáhne určité pravidelnosti v zásobování a mohou být redukovány nadbytečné zásoby ve všech svých podobách, od vstupního materiálu přes prázdné obaly až po hotové výrobky. Zásobovací vozíky ve své podstatě jezdí po předem stanovených trasách podle časově přesného jízdního řádu. Otázkou je, jak správně takový jízdní řád nastavit.
V případě, že nevyužíváme milk run a zásobování pracovišť provádíme přímou odvolávkou a přímým závozem jednoho pracoviště, můžeme se v naší úloze ptát, kolik budeme potřebovat manipulačních prostředků, což je úloha velice podobná. Ale zpět k stanovení časové náročnosti okruhu závozu v metodě milk run. Předně musíme stanovit postup, na základě kterého budeme mapovat a navrhovat změny a zlepšení stávajícího stavu, či zda budeme navrhovat okruhy zcela znovu.
Prvým krokem je přesné vydefinování činnosti realizované řidičem vláčku. Celý proces byl rozdělen na základní činnosti, kterým byly přiřazeny mezní body. Pro ukázku uvedeme jen některé:
- jízda vláčku,
- nakládka materiálu – uchopení obalu (prázdného KLT nebo plného obalu – krabice, pytel, apod.), u prázdné KLT její naplnění, naložení do vláčku,
- mezní bod – začátek činnosti UCHOPENÍ OBALU,
- mezní bod – začátek činnosti UCHOPENÍ DALŠÍHO OBALU nebo,
- mezní bod – začátek činnosti JÍZDA (rozjezd vláčku a jeho jízda) nebo,
- mezní bod – začátek další činnosti (úklid, zaskladnění materiálu, apod.),
- vykládka materiálu,
- zaskladnění materiálu.
Druhým krokem je časové určení všech činností. Při realizaci časových snímků se vyhodnocují krom potřebného času na realizaci činností i činnosti ztrátové, které jsou poslední kategorií činností prováděných pracovníky vláčku. Na základě nalezení a identifikace těchto ztrátových činností je možné okruhy jednotlivých vláčků zefektivňovat nebo ,chceme-li, optimalizovat. Rozdělíme je na dvě kategorie, a to na:
- nezaviněné – přestávka, diskuze s pracovníky, osobní potřeby, apod.,
- zaviněné – kouření, předčasný odchod na přestávku, apod.
Výsledkem tohoto kroku je stanovení potřebného času, stanovené normy, pro realizaci konkrétních činností pracovníka obsluhujícího vláček.
Posledním krokem je určení sekvence činností, které pracovník vláčku vykonává. V případě, že do této sekvence přiřadíme každé činnosti stanovenou normu, získáme celkový čas potřebný pro realizaci okruhu vláčku.
Výše uvedený postup je ovšem realizovatelný pouze do určité složitosti logistického systému. Tam kde logistický systém začne být příliš rozsáhlý a dostáváme se nad přibližně sedm jízdních tras vozíků, je nutné využít sofistikovanější metody výpočtu, protože výše uvedené matematické propočty nejsou schopny zachytit okolní pravděpodobnostní vlivy a pracují pouze s určitým průměrem čísel. Zde bych doporučil využít metody simulačních modelů a experimentů, které nám umožňují zachytit pravděpodobnost výskytu určitých stavů a dokážou na ně svým chováním i reagovat.
![]() |
Michal Šimon Autor, Doc. Ing. Michal Šimon, Ph.D., působí jako vedoucí katedry průmyslového inženýrství a managementu Západočeské univerzity v Plzni. Má dlouholeté zkušenosti s tvorbou praktických projektů z logistiky, výrobních layoutů, hmotných toků ve výrobě a racionalizace pracovišť. |


23.9. | PragVue 2025 |
23.9. | Virtuální konference Jak splnit nový zákon o kybernetické... |
25.9. | Cyber Attacks 2024 |
1.10. | Cyber Attacks 2025 |
21.10. | Bezpečnosť a dostupnosť dát 2025 |
Formulář pro přidání akce
13.8. | Webinář: Jak efektivně řídit obchodní aktivity ve firmě?... |
29.9. | The Massive IoT Conference |