- Přehledy IS
- APS (20)
- BPM - procesní řízení (23)
- Cloud computing (IaaS) (10)
- Cloud computing (SaaS) (31)
- CRM (52)
- DMS/ECM - správa dokumentů (20)
- EAM (17)
- Ekonomické systémy (68)
- ERP (75)
- HRM (28)
- ITSM (6)
- MES (33)
- Řízení výroby (36)
- WMS (28)
- Dodavatelé IT služeb a řešení
- Datová centra (25)
- Dodavatelé CAD/CAM/PLM/BIM... (41)
- Dodavatelé CRM (38)
- Dodavatelé DW-BI (50)
- Dodavatelé ERP (66)
- Informační bezpečnost (48)
- IT řešení pro logistiku (45)
- IT řešení pro stavebnictví (26)
- Řešení pro veřejný a státní sektor (27)


















![]() | Přihlaste se k odběru zpravodaje SystemNEWS na LinkedIn, který každý týden přináší výběr článků z oblasti podnikové informatiky | |
![]() | ||
Zkracování přestavovacích časů ve výrobní lince
Stále více výrobních podniků trápí časy pro přestavení výrobních linek. Jedná se o dobu potřebnou od ukončení původní výroby po rozjetí té nové, která zahrnuje čas na odstranění starého nářadí a přípravků, nastavení nového nářadí a doladění parametrů procesů až po výrobu prvního kusu. Aby nevznikaly prostoje a neklesala produktivita, je cílem dosáhnout co možná nejkratšího času pro přestavbu výrobních linek. V tomto článku si představíme metodiku SMED, která se právě na tuto optimalizaci zaměřuje.


Při změnách a seřizování se často plýtvá časem a prostoje strojů jsou v důsledku této skutečnosti delší.
Plýtvání u změny výroby je možné rozdělit do čtyř hlavních skupin:
- plýtvání při přípravě na změnu,
- plýtvání při montáži a demontáži,
- plýtvání při doseřízení a zkouškách,
- plýtvání při čekání na zahájení výroby. [3]
K řešení problému zkracování času pro seřizování a změny již v minulosti přistoupil japonský průmyslový inženýr Shigeo Shingo, který byl jedním ze zakladatelů výrobního systému Toyota. Téměř dvacet let vyvíjel a zdokonaloval metodu SMED (Single Minute Exchange of Die) pro rychlé změny. Dle Shinga lze pomocí této metody v praxi realizovat snížení času v průměru na 1/50 původní doby. Zkušenost s výměnou nástrojů ve firmě Mazda vedla Shinga k myšlence systému SMED, kdy je nutné rozdělit operace do dvou základních kategorií:
- Interní operace (IED) – neboli činnosti v klidu stroje, např. vlastní seřizování nástroje, které je možno provádět v případě zastavení stroje.
- Externí operace (OED) – neboli činnosti v záběhu stroje, např. doprava do skladu nebo příprava nástroje u stroje, tyto operace mohou být prováděny i při chodu stroje.
Metoda SMED se využívá na pracovištích, kde se často provádí seřizování a časy na seřízení představují velké a významné ztráty z kapacity stroje nebo linky. Seřizování strojů se obecně skládá z přípravy a kontroly nástrojů a materiálu (30 % času), montáže a výměny nástrojů a přípravků (5 % času), vlastního seřizování rozměrů a polohy nástrojů (15 % času) a odzkoušení a následné úpravy (50 % času). [1]
SMED na výrobní lince
Přestavení výrobní linky je proces, který se skládá z celé řady dílčích operací. Tyto operace musí být jednoznačně definovány a standardizovány. Nesmí jít o žádnou zvláštní činnost ponechanou osobním dovednostem pracovníků (operátorům na lince), ale o proces, který by měl být přesně standardizován. V následujícím textu se podíváme na reálný projekt, kterým nastíníme, jak může metodika SMED fungovat při optimalizaci prací na výrobní lince. V rámci SMED byl stanoven tento postup:
- zaznamenání současného stavu
- zaznamenání činností a průběhu měření
- časový model
- analýza
- vytvoření nového pracovního postupu
- vytvoření pracovního modelu
- odstranění úzkých míst – vytvoření nových technických řešení
- vytvoření nového časového modelu
- implementace nového řešení
- odzkoušení nového pracovního postupu
- vyhodnocení nového pracovního postupu
- vytvoření seznamu rizik
Zaznamenání současného stavu
Základním krokem bylo provedení prvotní analýzy a soupis činností, které byly probrány přímo s pracovníky. Tím došlo ke vzniku seznamu činností, které byly vykonávány během přestavby linky. Poté bylo pořízeno značné množství audiovizuálního záznamu, který byl následně velmi důsledně analyzován a porovnán se soupisem činností. Na tomto základě byly vypracovány podrobné seznamy činností pro každého pracovníka na výrobní lince, kde bylo jednoznačně vymezeno, co člověk dělá a jak dlouho mu to trvá. Na základě všech náměrů a propočtů byl vytvořen skutečný časový model, který popisuje, kolik člověko-minut je při přestavbě produktivních a kolik je neproduktivních. Ukázka modelu je znázorněna na obrázku 1.
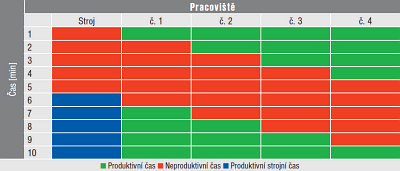
Obr. 1: Původní časový model (40 produktivních a 40 neproduktivních minut)
Analýza, vytvoření nového pracovního postupu
Po zaznamenání současného stavu jsme již věděli, jakým způsobem probíhá přestavba, jaká jsou její problematická a úzká místa a právě na tato místa jsme se zaměřili. V prvé řadě jsme provedli analýzu s cílem sumarizovat a roztřídit externí a interní činnosti a následně odstranit ztrátové časy. Součástí této analýzy bylo zároveň přiřazení klíčových činností k profesím. Do značné míry docházelo k tomu, že pracovníci s vyšší odborností prováděli i méně odborné práce, což způsobovalo problémy při organizaci přestavby linky. Tato analýza byla opět vyhodnocena ve vztahu ke konkrétním profesím jakožto samotné měření. Ukázka nového postupu na jednom z analyzovaných pracovišť je k vidění na obrázku 2.
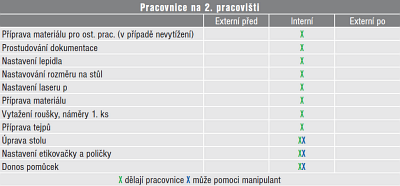
Obr. 2: Ukázka seznamu činností, pracoviště č. 1 nové
Analýza a odstranění úzkých míst
Na základě této analýzy byl definován nový pracovní model, kde hlavní úsporou bylo vytvoření tzv. bufferu, který umožnil dosažení stavu, kdy nedocházelo k současnému zastavení linky a stroje linku zásobujícího. S využitím bufferu jsme docílili předzásobení linky, přičemž následně se začal přestavovat stroj zásobující linku, ale linka, která měla možnost brát polotovary z bufferu, mohla v důsledku této skutečnosti stále vyrábět. Na obrázku 3 je zobrazeno technické řešení bufferu.
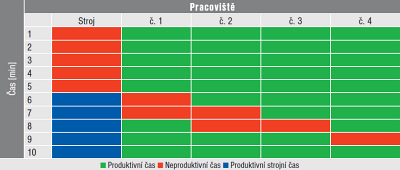
Obr. 3: Nový časový model (68 produktivních a 12 neproduktivních minut)
Implementace změn a odzkoušení 1
Po realizaci těchto změn ve formě změny pracovního postupu, nových technických řešení, změny organizační struktury a dalších drobných technických úprav bylo provedeno opětovné měření a zdokumentování nového stavu. Výsledkem bylo zásadní zkrácení doby přestavby.
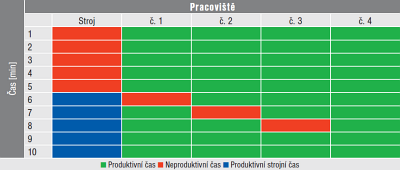
Obr. 4: Výsledný časový model přestavby (68 produktivních a 12 neproduktivních minut)
Definování nových úzkých míst
Po odstranění původních úzkých míst se ukázala místa nová prodlužující čas přestavby. Do jisté míry lze konstatovat, že tento postup je možné opakovat tak dlouho, dokud potenciální odstranění úzkých míst nepřinese zásadní úspory. Novým úzkým místem se stalo přestavení jednoho z pracovišť, na kterém se provádělo přesné značení polohy pomocí laseru. V tomto případě byla navržena taková opatření, abychom mohli toto úzké místo ovlivňující i další pracoviště, odstranit. Bylo navrženo takové technické řešení, které umožnilo tuto, na přestavbu složitou technologii zcela odstranit a nahradit ji jednodušší a levnější technologií.
Výsledný časový model přestavby
Komplexní odladění systému přestavby včetně všech navržených technických řešení a vytrénování pracovníků, aby jednoznačně dodržovali nový pracovní postup, přineslo velmi zásadní snížení času přestavby (obrázek 5).
Z časových modelů je zřejmé, že nově navržená metodika odvozená z metody SMED a aplikovaná na výrobní linky přináší zásadní zlepšení. Toto zlepšení se pak promítne nejen jako zvýšení produktivity, ale co je důležitější, dojde ke zvýšení flexibility, která přinese nové možnosti v oblastech řízení výroby. Celkově je možné konstatovat, že tato zlepšení a změny budou tak zásadní, že se mohou případně promítnout i jako jistá konkurenční výhoda na trhu.
Zdroje:
- A Revolution in Manufacturing: The SMED System
- Košturiak, J., Frolík, Z. 2006. Štíhlý a inovativní podnik. Praha: Alfa Publishing.
- Košturiak, J. 2010 Kaizen: osvědčená praxe českých a slovenských podniků. Brno: Computer Press.
Ing. Marek Bárdy


![]() ![]() | ||||||
Po | Út | St | Čt | Pá | So | Ne |
1 | 2 | 3 | 4 | 5 | 6 | |
7 | 8 | 9 | 10 | 11 | 12 | 13 |
14 | 15 | 16 | 17 | 18 | 19 | 20 |
21 | 22 | 23 | 24 | 25 | 26 | 27 |
28 | 29 | 30 | 31 | 1 | 2 | 3 |
4 | 5 | 6 | 7 | 8 | 9 | 10 |
11.7. | CyberEdu Letní škola |
23.9. | PragVue 2025 |
1.10. | Cyber Attacks 2025 |
21.10. | Bezpečnosť a dostupnosť dát 2025 |
11.11. | Umělá inteligence v IT infrastruktuře 2025 |
Formulář pro přidání akce
29.9. | The Massive IoT Conference |