- Přehledy IS
- APS (20)
- BPM - procesní řízení (23)
- Cloud computing (IaaS) (10)
- Cloud computing (SaaS) (32)
- CRM (52)
- DMS/ECM - správa dokumentů (20)
- EAM (17)
- Ekonomické systémy (68)
- ERP (76)
- HRM (28)
- ITSM (6)
- MES (34)
- Řízení výroby (36)
- WMS (29)
- Dodavatelé IT služeb a řešení
- Datová centra (25)
- Dodavatelé CAD/CAM/PLM/BIM... (41)
- Dodavatelé CRM (38)
- Dodavatelé DW-BI (50)
- Dodavatelé ERP (68)
- Informační bezpečnost (50)
- IT řešení pro logistiku (45)
- IT řešení pro stavebnictví (26)
- Řešení pro veřejný a státní sektor (27)


















![]() | Přihlaste se k odběru zpravodaje SystemNEWS na LinkedIn, který každý týden přináší výběr článků z oblasti podnikové informatiky | |
![]() | ||
Řízení procesní výroby a metoda TOC Pull Replenishment
Označení procesní výroba je z určitého úhlu pohledu zavádějící, protože její název jakoby chtěl zdůraznit, že právě v ní hrají důležitou roli procesy. Jenže copak v jiné výrobě procesy nemáme? Vždyť například v automobilové výrobě, která se, až na výjimky, vůbec neřadí k procesní výrobě, hrají procesy naprosto klíčovou roli… Ponechme ale stranou někdy lehce zavádějící název a pojďme se podívat, jak řídit tzv. procesní výrobu pomocí metody TOC.


Typy výroby podle VAT analýzy
TOC používá pro základní rozlišení typu výroby poměrně striktně tzv. VAT analýzu výroby – podle této analýzy lze každou výrobu rozdělit na nějakou dále již nedělitelnou jednotku, kde tato jednotka je typu V, A nebo T. Typy výroby V, A a T jsou specifické, navzájem neslučitelné a každý z nich se řídí jinak, resp. pro úspěšné uřízení každého z nich je třeba použít jiného přístupu. Celá výroba v daném podniku pak bývá kombinací několika typů výroby.
Pro ilustraci – například pivovar je kombinací typů V a T. V prvním kroku (výroba typu V) se vyrobí z několika málo základních surovin v několika krocích hlavní produkt (pivo konkrétní barvy, stupňovitosti a chuti). Různé hlavní produkty se vyrábějí obvykle v kampaních/šaržích, které po sobě jdou v určitém pořadí (nastavovací časy jsou závislé na pořadí – obvykle barva a stupňovitost), tj. nelze okamžitě vyrobit konkrétní pivo, výroba se opakuje vždy po nějakých intervalech. Hlavní výrobky (různá piva) se v dalším kroku (výroba typu T) spojují s dalšími komponenty v poměrně širokou paletu finálních výrobků, tj. konkrétní pivo stočené do sudu, láhve nebo do plechu, opatřené etiketou podle prodejce, v dané řeči nebo podle místních předpisů.
Procesní výroba patří téměř vždy do typu V, který je charakterizován tím, že na výstupu je velké množství finálních výrobků (nebo polotovarů), naopak na vstupu je jen velmi malé množství vstupních materiálů (v porovnání s výstupem), výrobní technologie a stupně výroby (stroje, pracoviště) jsou jednoúčelové (a s nulovou nebo jen velmi malou možností záměny nebo kapacitního rozšíření, navíc rozšíření je většinou investičně velmi náročné), ale především, většina výrobků nebo polotovarů musí při výrobě projít všemi stupni výroby v daném pořadí (pokud se tak nestane, tak se vyrobí jiný výrobek nebo zmetek). Navíc, ve většině případů zde existuje nějaký předpis pro technologickou dávku. Nedodržení alespoň minimální dávky má většinou opět za následek buď nefunkčnost technologie (výrobek nelze vyrobit), nebo zmetek (proces vyžaduje nějaké kritické množství k tomu, aby správně proběhl).
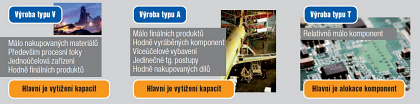
Co je na řízení procesní výroby zajímavého?
V první řadě je to prostředí, kde z definice funguje úzké místo téměř přesně tak, jak si jej představujeme – má nějakou konečnou kapacitu zpracování, která se sice může lišit pro různé výrobky, které danou technologií prochází, ale málokdy, pokud je to vůbec možné, se přesouvá na nějakou jinou technologii/stupeň výroby. Navíc podniky s výrobou typu V se snaží, aby úzké místo svoji polohu pokud možno vůbec neměnilo. Z tohoto pohledu je to tedy poměrně stabilní prostředí pro nastavení plánovacích procesů a rozhodovacích kritérií. Protože platí, že naprostá většina výrobků prochází přes téměř všechny výrobní stupně, můžeme se na takovou výrobu dívat v podstatě jako na linku (co do ní na jedné straně vstoupí, to z druhé strany vystoupí).
Komplikací může být pár skutečností, ke kterým v reálném životě dochází:
- Nejužší místo je hned na začátku nebo naopak až na konci výroby. Dopad variability procesů a poruch na poslední operaci je v delší sekvenci na sebe navazujících operací vždy větší než v kratší sekvenci operací. Ideální je z pohledu plánování, když úzké místo je někde uprostřed, pro spolehlivost procesů platí podmíněná pravděpodobnost…
- Existují tzv. na sobě závislá seřízení/přestavení technologie – různé pořadí výrobků procházejících po sobě vede k různě dlouhým nastavovacím časům (= existuje pořadí s nejlepším a nejhorším využitím technologie, pokud za využití budeme brát spotřebu času).
- Po průchodu každým výrobním stupněm je možné polotovar získaný tímto stupněm zpracovat v následujícím stupni mnoha různými způsoby (= vzniknou další, rozdílné polotovary), vzniká tedy ideální prostředí pro tzv. „vykrádání materiálu“ v zakázce.
- Tržní poptávka/spotřeba některých výrobků je tak malá, že se nevyplatí je vyrábět v každém výrobním cyklu.
- Co uděláme s údržbou a opravami? Když se zastaví jedna technologie, stojí zpravidla celá výroba, málokdy je mezi stupni tolik prostoru, aby se tam mohla hromadit nedokončená výroba (podobnost s linkami JIT v automotive).
Pojďme se na jednotlivé případy podívat optikou TOC.
Poloha úzkého místa
Ať je úzké místo kdekoliv, stále platí základní poučky pro využití úzkého místa a podřízení ostatních zdrojů:
- Kapacita je správně využita jen v případě, že zdroj pracuje na zakázce s termínem dodání v horizontu průběžné doby daného typu zakázek.
- Úkolem neúzkých míst je pracovat tak, aby plynule zásobila prací omezení (buď buffer zakázek před skutečným úzkým místem, nebo trhem, který je omezením vždy).
Z tohoto pohledu se poloha úzkého místa na začátku výroby zdá být výhodnější, protože pro správné vytížení úzkého místa stačí mít správnou frontu zakázek a dostatek materiálu. Problémem může být splnění termínu dodání včas, protože zakázka sice projde bez problémů úzkým místem, ale pak může mít potíže v průběhu zbylé výroby – při konkrétní míře variability procesů ve výrobě se může stát, že některá ze zakázek neprojde všemi výrobními stupni včas a nestihne termín dodávky. Naopak úzké místo na konci výroby se může zdát jako problém, protože pro správné využití úzkého místa musí zakázky projít celou výrobou, a při konkrétní míře variability procesů ve výrobě se může stát, že některá ze zakázek neprojde všemi výrobními stupni včas a dojde k prostojům na úzkém místě, a ve svém důsledku ke zpoždění termínu dodání. Všimněte si, že ať je úzké místo na začátku nebo na konci výroby, dopad je vždy stejný – může mít vliv na spolehlivost výroby.
Z pohledu TOC existuje jediné řešení – mírně upravit (= prodloužit) průběžnou dobu výroby (tzv. lano), tj. uvolnit zakázku do výroby o něco dříve vůči termínu dodání, než by tomu bylo v případě, že úzké místo je někde uprostřed výroby. Efektem prodloužení lana je to, že zakázka má v průchodu výrobou dostatek času na zvládání případných poruch.
Závislá seřízení
Pokud existuje situace, že na úzkém místě čas přenastavení z výrobku A na výrobek B se podstatně liší od času přenastavení místa z výrobku B na výrobek A, a takto je tomu v praxi pro většinu kombinací výrobků, pak máme problém. Nemůžeme zařazovat za sebe libovolné výrobky v libovolném pořadí, aniž by to mělo vliv na zvýšené prostoje, a tudíž na výkonnost a ziskovost celé výroby.
V tomto případě pak ale existuje tzv. ideální sekvence zakázek, která zajistí, že přenastavení mezi dvěma po sobě jdoucími výrobky je minimální. Tudíž je možné postavit výrobní plán, který zajistí maximální průchodnost výroby a rovněž i maximální možnou ziskovost (celé továrny) při daném produktovém mixu. Vedlejším efektem je, že jeden a ten samý výrobek se v plánu objeví jen jednou ve výrobním cyklu. Cykly se opakují, říká se jim také výrobní kampaň (nebo prostě jen kampaň nebo šarže).
Problémem je, že ačkoli se výrobek fyzicky vyrábí např. jen několik hodin nebo směn, jeho průběžná doba dodání je zpravidla významně delší, rovná se jednomu cyklu, jednomu opakování všech výrobků, tj. pokud máme například 50 výrobků a každý se vyrábí v průměru jeden den, tak je doba opakování cyklu a tím pádem i nejdelší doba dodání 50 dní. Pokud je tato situace pro trh nepřijatelná, je třeba řešit zásobování trhu formou výroby na sklad. V této situaci je výhodné pro řízení skladu zavést TOC Pull Replenishment, které díky svým vlastnostem dokáže lépe využít výrobní linku(y).
Kradení materiálu
K vykrádání materiálu mezi zakázkami dochází vždy, pokud v podniku přežívá syndrom efektivity. Díky variabilitám v průběhu výroby se může stát, že do určitého bodu doteče určité množství materiálu, ale v dalším kroku jej nelze z nějakého důvodu zpracovat původně zamýšleným způsobem. Aby technologie nestála (a nevznikly prostoje zařízení = ztráta vytíženosti/efektivity), vezme se dokončený polotovar a zpracuje se na něco jiného (např. v papírně, role konkrétního druhu papíru se rozřeže na jiný formát, než bylo původně plánováno, vznikne tak jiný výrobek/polotovar). Původní zakázka (pro kterou byl polotovar vyráběn) již nemůže být splněna, dochází ke zpoždění, někdy velmi významnému (než se znovu vyrobí původní polotovar). Výsledkem je významné ohrožení spolehlivosti dodacích termínů a zvýšení skladových zásob.
Řešení je jednoduché – jednak to znamená eliminovat ve výrobě tlak na efektivitu a nahradit jí tzv. Full Kit přístupem – mentalita a proces založené na tom, že ke každému výrobnímu kroku je vždy zajištěna veškerá příprava, jak je naznačeno už názvem Full Kit = úplný balíček přípravy. Dalším opatřením je přesný předpis spotřeby materiálu jednotlivými operacemi na jednotlivých stupních, aby nemohlo dojít ke spotřebování „nesprávného materiálu“, a důsledné dodržování plánu. Ze zřejmých důvodů zavedení pravidel a procesu Full Kit má větší vliv než přesný popis spotřeby.
Rozdílnost poptávky po různých produktech
Pokud jednorázové objednávky zákazníků za určité období jsou (výrazně) menší než minimální množství, které lze vyrobit za dobu cyklu, tak máme jen pár možností:
- výrobek vyrobit a neprodané množství výrobku uskladnit (může být potíž v případě, že výrobek má krátkou expiraci nebo má např. barevný odstín),
- nevyrábět vůbec (nevyplatí se nám),
- přezkoumat velikost výrobní dávky a zmenšit ji (pokud to jde).
Oprava a údržby
Ve výrobě typu V je problém vždy, když dojde k poruše jednoho zdroje, zdroje za sebou navazují a delší výpadek jednoho zdroje znamená zastavení celé výroby. Dobrým řešením je určitě zavedení TPM, pokud výroba vyrábí na sklad, pak zavedení TOC Pull Replenishment ve spojení s TPM má opět významný vliv na maximalizaci průtoku výrobou.
Z pohledu TOC se řízení procesní výroby nijak neodlišuje od řízení jakékoliv jiné výroby – stále zde existují buffery, stále zde existuje řízení bufferů (buffer management – dále jen BM) a řízení výroby na různých pracovištích pomocí fronty práce prioritizované podle signálů BM (spotřeby bufferu). Výjimku představují výše uvedené situace a jejich řešení je obvykle implementováno jak do TOC softwaru, tak do příslušných pravidel a postupů, kterými se pak systém řídí. Zajímavé je zavedení metody TOC Pull Replenishment, která zde byla několikrát zmíněna.
Pokud výroba vyrábí na sklad, což je ve většině procesních výrob výhodné z pohledu vytížení a řízení výrobních kampaní, tak nutně dochází k situacím, že výrobky, které se tzv. „točí“, na skladě nejsou (zásoba vyschne dříve, než se v daném cyklu výrobek opět vyrobí a doplní na sklad), zatímco výrobků s nízkou spotřebou je ve skladu více, než je třeba. (Samozřejmě, protože málokterý plánovač a ředitel výroby si dovolí nezařadit v daném cyklu všechny výrobky – ale pro některé je prostě i minimální výrobní dávka větší, než je třeba. A navíc, co kdyby se náhodou spotřeba zvýšila…?)
TOC Pull Replenishment využívá konceptu tzv. skladových bufferů, jinak také cílů zásob. Každý produkt na každém skladě má svůj cíl zásob – podle definice množství, která odpovídá maximální realistické spotřebě za dobu doplnění zásob. Tudíž produkty, které se točí (dále jen bestsellery), musí mít vyšší cíl zásob (dále jen buffer) než ty, které se neprodávají (dále jen ležáky). Doba doplnění zásob je pro všechny stejná, je to doba cyklu.
Většinou platí, že jak bestseller, tak ležák mají zhruba stejnou minimální výrobní dávku a často i dobu seřízení. Jediný rozdíl při řízení je pak ve skutečné velikosti výrobní dávky, která se na technologii naplánuje a pak vyrábí.
Pro většinu plánovacích systémů je v takové situaci nastaveno, že pokud zásoba poklesne pod MIN, naplánuje se nová výrobní dávka (bez ohledu na to, jaká je spotřeba). Pro TOC Pull Replenishment je to jinak. TOC Pull Replenishment v průběhu spotřeby sleduje, jak se spotřebovává buffer, a zaznamenává tzv. penetraci bufferu (kolik chybí zásob proti plnému skladu, cíli zásob). Každý buffer je rozdělen na tři díly (ideálně třetiny) a každý díl má svoji barvu (pro jednoduchost vizuálního řízení):
- třetina – penetrace 0–33 % – barva zelená – význam => zásob máme dost
- třetina – penetrace 34–66 % – barva žlutá – význam => zásob máme tak akorát
- třetina – penetrace 67–100 % – barva červená – význam => skoro nemáme zásoby
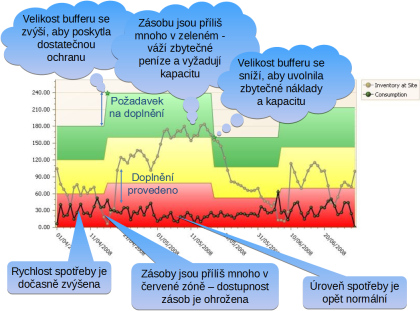
Udržování správné úrovně zásob
Kromě toho jsou tu ještě dvě barvy – azurová (penetrace < 0 %), což znamená, že máme více zásob, než jsme kdy chtěli (OverStock), a pak černou (penetrace > 100 %), což znamená, že je sklad prázdný (StockOut).
Pokud proces BM vyhodnotí, že se buffer spotřebovává příliš rychle (roste spotřeba), nebo příliš pomalu (klesá spotřeba), dá pokyn ke zvýšení nebo snížení bufferu o 1/3. Tím se změní i velikost zón bufferu.
Buffer je vždy nastaven tak, aby co nejlépe odpovídal aktuální spotřebě daného výrobku. Zásoby se vždy doplňují na plný buffer – buffer vždy obsahuje aktuální skladové množství (zásoba na skladě) a množství, které je na cestě do skladu (zásoba na cestě nebo zásoba ve výrobě), rozdíl je množství, které ve skladu chybí a je třeba jej do skladu doplnit. Ve výrobě je to velikost příští výrobní objednávky (v nákupu velikost příští nákupní objednávky). Výrobní objednávka v okamžiku vydání si s sebou nese i stav bufferu v okamžiku vydání.
Navrhovanou velikost výrobní objednávky je tak možné přímo při zaplánování srovnat s minimálním množstvím a také s urgencí toho, jestli je vůbec nutné dané množství vyrábět. Popsaný přístup lze ukázat na obrázku 5.
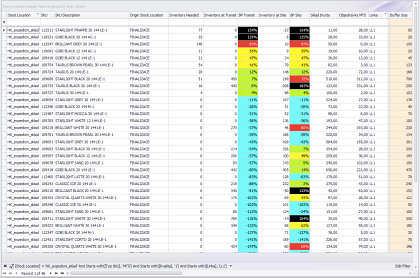
Pravý barevný sloupec označuje stav skladu (disponibilní zásobu), levý barevný sloupec označuje stav skladu po zaplánování. Pouze tři produkty potřebují urgentně doplánovat (a vyrobit), navrhované množství je ale zatím významně menší než minimální výrobní dávka. Většina ostatních je naopak naplánována ve výrazně větším množství (příprava na odstávku).
Shrnutí
Pomocí přístupu TOC Pull Replenishment je možné procesní výrobu významně lépe propojit s reálnou potřebou trhu, to znamená výrazně lépe využít dostupnou kapacitu i přes existenci výše zmíněných překážek. Ve výrobě tak lze maximalizovat vytížení kapacity vůči produktům, které firmě nejvíce vydělávají, a naopak omezit produkty, které nevydělávají. V praxi se to odráží hlavně na struktuře skladů, omezí se vznik přebytků a nedostatků na skladě, lze naplánovat výši skladů, která by umožnila provedení oprav a odstávek, s minimální ztrátou obratu po dobu oprav/odstávek. TOC Pull Replenishment rovněž umožňuje lepší rozhodnutí o úpravě velikosti dávek ve výrobě, což vede ke zkrácení výrobního cyklu a tím dále posiluje konkurenceschopnost firmy – rychlost reakce na požadavek zákazníků, velikost a strukturu skladů a celkovou efektivitu výroby.
![]() |
Pavel Majer Autor článku je partnerem firmy Goldratt CZ, která se věnuje implementacím TOC v podnicích. |


Formulář pro přidání akce