- Přehledy IS
- APS (20)
- BPM - procesní řízení (23)
- Cloud computing (IaaS) (10)
- Cloud computing (SaaS) (32)
- CRM (52)
- DMS/ECM - správa dokumentů (20)
- EAM (17)
- Ekonomické systémy (68)
- ERP (76)
- HRM (28)
- ITSM (6)
- MES (35)
- Řízení výroby (36)
- WMS (29)
- Dodavatelé IT služeb a řešení
- Datová centra (25)
- Dodavatelé CAD/CAM/PLM/BIM... (41)
- Dodavatelé CRM (38)
- Dodavatelé DW-BI (50)
- Dodavatelé ERP (68)
- Informační bezpečnost (50)
- IT řešení pro logistiku (45)
- IT řešení pro stavebnictví (26)
- Řešení pro veřejný a státní sektor (27)
Partneři sekce
Tematické sekce


















Branžové sekce
![]() | Přihlaste se k odběru zpravodaje SystemNEWS na LinkedIn, který každý týden přináší výběr článků z oblasti podnikové informatiky | |
![]() | ||
Partneři webu
IT SYSTEMS 9/2010 , Plánování a řízení výroby
I v dnešní době vám spousta řídících pracovníků ve výrobě řekne, že nejlépe se výroba řídí pomocí ostré tužky a listu papíru formátu A0 nalepeného na rýsovacím prkně. S tím se dá samozřejmě leckdy těžko polemizovat, ale rostoucí vnější i vnitřní tlaky na zkracování dodacích lhůt, široký sortiment, kvalitu a minimalizaci cen výrobků nutí i zatvrzelé odpůrce systémů na řízení výroby změnit názor.
Informační systémy se při řízení a plánování výroby uplatňují ve všech jejich etapách, od technické přípravy přes plánování materiálů a kapacit, optimalizaci výrobních zakázek až po dílenské řízení výroby a vyhodnocování efektivity celého procesu.
Implementaci ERP systémů často provází jeden veliký problém, a to je kvalita dat. Začíná to u TPV dat, která obsahují špatné, často hrubě odhadované časy v technologických postupech, a končí u odpisu času a materiálu na výrobních zakázkách. Často se lze setkat s výrobními podniky, které chtějí spouštět plánovací procesy několikrát týdně, přestože vstupy z jednotlivých pracovišť jsou zpravidla zadávány po skončení pracovního týdne. Základním předpokladem nasazení systémů řízení výroby by tedy mělo být výrazné kvalitativní vylepšení datové základny, která je alfou i omegou úspěchu implementace. Lze tedy říci, že někdy k výraznému pokroku stačí pracovat s přesnými a aktuálními daty. Jakmile je tato základní podmínka splněna, lze uvažovat o nasazení pokročilejších integrovaných systémů a metod řízení výroby.
Na začátku stojí kvalitní technologická data. Ideálním řešením je propojení systémů pro design výrobků (CAD) se systémy pro správu dat výrobků (PDM) s ERP systémem za podpory dalších integrovaných podpůrných nástrojů například pro výpočty technologických časů. Celý tento systém je známý pod zkratkou PLM (product lifecycle management). Výsledkem synergie jsou reálná technologická data výrobků včetně zapracované zpětné vazby z výrobního procesu a systémů na řízení poprodejního servisu. S takovou datovou základnou je možné začít plánovat.
Samotný plánovací proces je možné rozdělit na část dlouhodobého a část krátkodobého plánování. V první části pracujeme především s výhledy a plány. Plánování vychází z příbuznosti výrobkových řad, zejména v zakázkové výrobě nebo u nových výrobků není k dispozici kompletní výrobní dokumentace, a tak jsou plánovány určité fiktivní finální výrobky (fantomy), které obsahují ve své struktuře pouze strategické polotovary a materiály. Výsledkem dlouhodobých plánů by mělo být zajištění materiálů a polotovarů s velmi dlouhou dobou pořízení, která podstatně ovlivňuje celkovou průběžnou dobu výroby finálních produktů. Samozřejmě je také nutné dbát na optimální skladové zásoby.
Plánování krátkodobé už vychází ze skutečných zakázek, objednávek, případně požadavků skladů v případě výroby na sklad. V této etapě také dochází ke spotřebování materiálů a polotovarů naplánovaných v dlouhodobé fázi. Zde se uplatňují především dvě základní metody plánování. Plánování materiálových požadavků (MRP) – je součástí informačních systémů více než padesát let. MRP spočívá ve shromáždění požadavků na zajištění finálních výrobků, jejich rozpad na polotovary a materiál dle všech úrovní kusovníku a porovnání s aktuální dostupností těchto položek na skladech i v plánovaných objednávkách nákupních, výrobních i přeskladňovacích. Z tohoto rozpadu vznikne časově rozlišený seznam položek, které je nutno zajistit u dodavatelů, nebo vlastní výrobou, případně výrobou v kooperaci. Dále je to kapacitní plánování CRP, které stanovuje kapacitní požadavky na zdroje, tedy pracoviště, stroje, výrobní linky a pracovníky. Stále více podniků používá plánování do skutečných kapacit, které zamezuje vzniku přetížení úzkých míst výrobních linek. Opět to ale klade již několikrát zmiňovaný důraz na reálnost dat o výrobních zdrojích. Je také vhodné propojení s podpůrnými systémy například na preventivní a opravnou údržbu (PCM), které dokážou aktualizovat skutečnou kapacitu v závislosti například na plánovaných odstávkách. V oblasti kapacitního plánování je často aplikována teorie omezení (TOC), která řeší hledání a odstraňování úzkých míst v podnikových procesech.
Po zafixování výrobního plánu, zajištění materiálů a polotovarů je efektivní nasazení takzvaných pokročilých metod plánování APS. Odlišnost od předchozích plánovacích procesů je především v tom, že výše uvedené metody plánování pracují pouze se třemi parametry: časem, množstvím a kapacitou. Naproti tomu dokážou APS systémy optimalizovat řazení zakázek podle mnoha dalších parametrů. Je to třeba prioritizace zakázek například podle důležitosti zákazníka nebo technologické podmínky, které ovlivňují mezioperační a seřizovací časy a vedou tak opět ke zkrácení průběžné doby výroby. APS systémy fungují většinou mimo standardní ERP systém. Z něho si přebírají data o výrobcích a výrobních zakázkách. Provedou optimalizaci podle nastavených priorit, případně vytvoří několik alternativních plánů s ohledem na nastavené parametry a po odsouhlasení výrobním dispečerem upraví v ERP systému řazení zakázek. K této oblasti jsou různé přístupy, od členění výrobních zakázek na tzv. mikrooperace, jejich sledování a zpětnou vazbu do APS až po druhý extrém, kterým je nahlížet na určitý sled operací jako na nedílný celek, který se řídí samovolně pouze na základě určitých předem stanovených omezení a cílů.
Poslední fází řízení a plánování výroby je dílenské řízení, kdy dispečer dostává pevně stanovený sled výrobních příkazů. Změny zde probíhají už pouze na základě aktuální situace například výpadků kapacit, zmetkovitosti, a jiných nepredikovatelných výpadků. Pro zajištění kvalitní a rychlé zpětné vazby je vhodné informační systém přivést až na konkrétní pracoviště. Interakce je pak zajištěna terminály, u kterých jednotliví pracovníci okamžitě registrují odvedené operace na výrobních zakázkách včetně případných odchylek a zajišťují tak kvalitní zpětnou vazbu pro výše uvedené procesy.
Přes nemalou schopnost informačních systémů zajistit řízení výroby automaticky zůstává stále velká odpovědnost na uživatelích. K tomu, aby jejich rozhodnutí byla odpovědná, potřebují především relevantní informace. Tato oblast je řešena celou řadou nástrojů nazývaných business intelligence. Jejich základními úkoly je monitorovat, analyzovat a plánovat podnikové procesy. Při monitorování stavu podniku se využívají dvě skupiny nástrojů: reportovací a on-line sledování klíčových ukazatelů výkonnosti. První ze zmiňovaných nabízejí široké možnosti pro vytváření, správu a používání sestav. Sestavy jsou vytvářeny v jednotném prostředí manuálně nebo pomocí průvodců. Sestavy je možno prohlížet, tisknout, exportovat do různých formátů, automaticky rozesílat elektronickou poštou v určitých časech, případně u dynamicky se měnících sestav je možné prohlížet jejich historii. Sledování klíčových ukazatelů neboli scorecarding je nástroj, který poskytuje okamžitý pohled na stav podniku v definovaných ukazatelích založených většinou na porovnání aktuálního stavu s plánovaným doplněných o grafické symboly a prezentovaných na podnikovém intranetu. Analytické nástroje na rozdíl od reportingu nezobrazují pouze určitý stav hodnot, ale pomáhají nám odpovědět na otázky typu: „Proč tato situace nastala?“ a „Co se bude dít dále?“ Základem analýzy jsou data z různých zdrojů, protože k dobré analýze potřebujeme nejen firemní data z informačního systému, ale je potřeba je doplnit i o další datové zdroje, které umožňují lepší stanovení trendů. Data jsou vhodně agregovaná a uložená ve formě tzv. OLAP (on-line analytical processing) kostek. Nedílnou součástí analýz služeb je datamining, což je komplex algoritmů a modelů sloužící k hledání závislostí mezi daty. Po analýze je logicky následují plánovací procesy. V této oblasti nám manažerské informační systémy nabízí velkou podporu při tvorbě plánů výroby, dlouhodobých výhledů apod. Samozřejmostí je automatické generování těchto plánů na základě údajů z minulých období a jejich extrapolace podle zjištěných trendů, simulace různých variant rozpočtů.
Přesné plánování a řízení výroby pomáhá optimalizovat výrobní proces z hlediska finančního i časového. Napomáhá také lepší koordinaci při spolupráci na složitějších výrobcích nebo investičních celcích. Pak je možné přistupovat k dekompozici výrobního procesu, jak to známe například z automobilového nebo leteckého průmyslu. Zajímavým příkladem je třeba rozdíl v průběžné době výroby letadel v americkém Everetu. Známý model 747, tzv. Jumbojet, se zde montuje z primárních dílů a jeho průběžná doba výroby je zhruba osm týdnů. Naproti tomu nejmladší z rodiny boeingů 787 Dreamliner je skládán z logických celků a průběžná doba činí pouze tři dny.
Autor je specialista na řešení Microsoft Dynamics pracující ve společnosti Microsoft.
Nové metody řízení výroby
Pavel Šlesingr
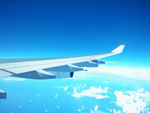


Informační systémy se při řízení a plánování výroby uplatňují ve všech jejich etapách, od technické přípravy přes plánování materiálů a kapacit, optimalizaci výrobních zakázek až po dílenské řízení výroby a vyhodnocování efektivity celého procesu.
Implementaci ERP systémů často provází jeden veliký problém, a to je kvalita dat. Začíná to u TPV dat, která obsahují špatné, často hrubě odhadované časy v technologických postupech, a končí u odpisu času a materiálu na výrobních zakázkách. Často se lze setkat s výrobními podniky, které chtějí spouštět plánovací procesy několikrát týdně, přestože vstupy z jednotlivých pracovišť jsou zpravidla zadávány po skončení pracovního týdne. Základním předpokladem nasazení systémů řízení výroby by tedy mělo být výrazné kvalitativní vylepšení datové základny, která je alfou i omegou úspěchu implementace. Lze tedy říci, že někdy k výraznému pokroku stačí pracovat s přesnými a aktuálními daty. Jakmile je tato základní podmínka splněna, lze uvažovat o nasazení pokročilejších integrovaných systémů a metod řízení výroby.
Na začátku stojí kvalitní technologická data. Ideálním řešením je propojení systémů pro design výrobků (CAD) se systémy pro správu dat výrobků (PDM) s ERP systémem za podpory dalších integrovaných podpůrných nástrojů například pro výpočty technologických časů. Celý tento systém je známý pod zkratkou PLM (product lifecycle management). Výsledkem synergie jsou reálná technologická data výrobků včetně zapracované zpětné vazby z výrobního procesu a systémů na řízení poprodejního servisu. S takovou datovou základnou je možné začít plánovat.
Samotný plánovací proces je možné rozdělit na část dlouhodobého a část krátkodobého plánování. V první části pracujeme především s výhledy a plány. Plánování vychází z příbuznosti výrobkových řad, zejména v zakázkové výrobě nebo u nových výrobků není k dispozici kompletní výrobní dokumentace, a tak jsou plánovány určité fiktivní finální výrobky (fantomy), které obsahují ve své struktuře pouze strategické polotovary a materiály. Výsledkem dlouhodobých plánů by mělo být zajištění materiálů a polotovarů s velmi dlouhou dobou pořízení, která podstatně ovlivňuje celkovou průběžnou dobu výroby finálních produktů. Samozřejmě je také nutné dbát na optimální skladové zásoby.
Plánování krátkodobé už vychází ze skutečných zakázek, objednávek, případně požadavků skladů v případě výroby na sklad. V této etapě také dochází ke spotřebování materiálů a polotovarů naplánovaných v dlouhodobé fázi. Zde se uplatňují především dvě základní metody plánování. Plánování materiálových požadavků (MRP) – je součástí informačních systémů více než padesát let. MRP spočívá ve shromáždění požadavků na zajištění finálních výrobků, jejich rozpad na polotovary a materiál dle všech úrovní kusovníku a porovnání s aktuální dostupností těchto položek na skladech i v plánovaných objednávkách nákupních, výrobních i přeskladňovacích. Z tohoto rozpadu vznikne časově rozlišený seznam položek, které je nutno zajistit u dodavatelů, nebo vlastní výrobou, případně výrobou v kooperaci. Dále je to kapacitní plánování CRP, které stanovuje kapacitní požadavky na zdroje, tedy pracoviště, stroje, výrobní linky a pracovníky. Stále více podniků používá plánování do skutečných kapacit, které zamezuje vzniku přetížení úzkých míst výrobních linek. Opět to ale klade již několikrát zmiňovaný důraz na reálnost dat o výrobních zdrojích. Je také vhodné propojení s podpůrnými systémy například na preventivní a opravnou údržbu (PCM), které dokážou aktualizovat skutečnou kapacitu v závislosti například na plánovaných odstávkách. V oblasti kapacitního plánování je často aplikována teorie omezení (TOC), která řeší hledání a odstraňování úzkých míst v podnikových procesech.
Po zafixování výrobního plánu, zajištění materiálů a polotovarů je efektivní nasazení takzvaných pokročilých metod plánování APS. Odlišnost od předchozích plánovacích procesů je především v tom, že výše uvedené metody plánování pracují pouze se třemi parametry: časem, množstvím a kapacitou. Naproti tomu dokážou APS systémy optimalizovat řazení zakázek podle mnoha dalších parametrů. Je to třeba prioritizace zakázek například podle důležitosti zákazníka nebo technologické podmínky, které ovlivňují mezioperační a seřizovací časy a vedou tak opět ke zkrácení průběžné doby výroby. APS systémy fungují většinou mimo standardní ERP systém. Z něho si přebírají data o výrobcích a výrobních zakázkách. Provedou optimalizaci podle nastavených priorit, případně vytvoří několik alternativních plánů s ohledem na nastavené parametry a po odsouhlasení výrobním dispečerem upraví v ERP systému řazení zakázek. K této oblasti jsou různé přístupy, od členění výrobních zakázek na tzv. mikrooperace, jejich sledování a zpětnou vazbu do APS až po druhý extrém, kterým je nahlížet na určitý sled operací jako na nedílný celek, který se řídí samovolně pouze na základě určitých předem stanovených omezení a cílů.
Poslední fází řízení a plánování výroby je dílenské řízení, kdy dispečer dostává pevně stanovený sled výrobních příkazů. Změny zde probíhají už pouze na základě aktuální situace například výpadků kapacit, zmetkovitosti, a jiných nepredikovatelných výpadků. Pro zajištění kvalitní a rychlé zpětné vazby je vhodné informační systém přivést až na konkrétní pracoviště. Interakce je pak zajištěna terminály, u kterých jednotliví pracovníci okamžitě registrují odvedené operace na výrobních zakázkách včetně případných odchylek a zajišťují tak kvalitní zpětnou vazbu pro výše uvedené procesy.
Přes nemalou schopnost informačních systémů zajistit řízení výroby automaticky zůstává stále velká odpovědnost na uživatelích. K tomu, aby jejich rozhodnutí byla odpovědná, potřebují především relevantní informace. Tato oblast je řešena celou řadou nástrojů nazývaných business intelligence. Jejich základními úkoly je monitorovat, analyzovat a plánovat podnikové procesy. Při monitorování stavu podniku se využívají dvě skupiny nástrojů: reportovací a on-line sledování klíčových ukazatelů výkonnosti. První ze zmiňovaných nabízejí široké možnosti pro vytváření, správu a používání sestav. Sestavy jsou vytvářeny v jednotném prostředí manuálně nebo pomocí průvodců. Sestavy je možno prohlížet, tisknout, exportovat do různých formátů, automaticky rozesílat elektronickou poštou v určitých časech, případně u dynamicky se měnících sestav je možné prohlížet jejich historii. Sledování klíčových ukazatelů neboli scorecarding je nástroj, který poskytuje okamžitý pohled na stav podniku v definovaných ukazatelích založených většinou na porovnání aktuálního stavu s plánovaným doplněných o grafické symboly a prezentovaných na podnikovém intranetu. Analytické nástroje na rozdíl od reportingu nezobrazují pouze určitý stav hodnot, ale pomáhají nám odpovědět na otázky typu: „Proč tato situace nastala?“ a „Co se bude dít dále?“ Základem analýzy jsou data z různých zdrojů, protože k dobré analýze potřebujeme nejen firemní data z informačního systému, ale je potřeba je doplnit i o další datové zdroje, které umožňují lepší stanovení trendů. Data jsou vhodně agregovaná a uložená ve formě tzv. OLAP (on-line analytical processing) kostek. Nedílnou součástí analýz služeb je datamining, což je komplex algoritmů a modelů sloužící k hledání závislostí mezi daty. Po analýze je logicky následují plánovací procesy. V této oblasti nám manažerské informační systémy nabízí velkou podporu při tvorbě plánů výroby, dlouhodobých výhledů apod. Samozřejmostí je automatické generování těchto plánů na základě údajů z minulých období a jejich extrapolace podle zjištěných trendů, simulace různých variant rozpočtů.
Přesné plánování a řízení výroby pomáhá optimalizovat výrobní proces z hlediska finančního i časového. Napomáhá také lepší koordinaci při spolupráci na složitějších výrobcích nebo investičních celcích. Pak je možné přistupovat k dekompozici výrobního procesu, jak to známe například z automobilového nebo leteckého průmyslu. Zajímavým příkladem je třeba rozdíl v průběžné době výroby letadel v americkém Everetu. Známý model 747, tzv. Jumbojet, se zde montuje z primárních dílů a jeho průběžná doba výroby je zhruba osm týdnů. Naproti tomu nejmladší z rodiny boeingů 787 Dreamliner je skládán z logických celků a průběžná doba činí pouze tři dny.
Autor je specialista na řešení Microsoft Dynamics pracující ve společnosti Microsoft.
Chcete získat časopis IT Systems s tímto a mnoha dalšími články z oblasti informačních systémů a řízení podnikové informatiky? Objednejte si předplatné nebo konkrétní vydání časopisu IT Systems z našeho archivu.


IT Systems podporuje
Formulář pro přidání akce
Další vybrané akce
16.9. | ICT snídaně: Moderní HR procesy: Rychlejší, přehlednější,... |
16.9. | Microsoft & Veeam Security Roadshow – Bratislava... |
23.9. | IT konference: Arrow Forum 2025 |
29.9. | The Massive IoT Conference |