- Přehledy IS
- APS (20)
- BPM - procesní řízení (23)
- Cloud computing (IaaS) (10)
- Cloud computing (SaaS) (32)
- CRM (52)
- DMS/ECM - správa dokumentů (20)
- EAM (17)
- Ekonomické systémy (68)
- ERP (75)
- HRM (28)
- ITSM (6)
- MES (34)
- Řízení výroby (36)
- WMS (29)
- Dodavatelé IT služeb a řešení
- Datová centra (25)
- Dodavatelé CAD/CAM/PLM/BIM... (41)
- Dodavatelé CRM (38)
- Dodavatelé DW-BI (50)
- Dodavatelé ERP (68)
- Informační bezpečnost (49)
- IT řešení pro logistiku (45)
- IT řešení pro stavebnictví (26)
- Řešení pro veřejný a státní sektor (27)


















![]() | Přihlaste se k odběru zpravodaje SystemNEWS na LinkedIn, který každý týden přináší výběr článků z oblasti podnikové informatiky | |
![]() | ||
Štíhlá logistika
Pojem štíhlá logistika je pro většinu z nás podstatně méně známým a méně určitým než pojem štíhlá výroba. S pojmem štíhlé výroby jsme se téměř všichni setkali a jsme schopni si představit řadu metod, které jsou v dané oblasti používány. Nad problematikou štíhlosti a jejího hledání se je však nutno zamýšlet komplexněji. Všechny zmíněné pojmy společně vytvářejí tzv. lean enterprise, tedy štíhlý podnik. Pod tímto pojmem se ovšem skrývá spíše štíhlé myšlení v podniku, a tak by bylo chybou považovat za štíhlý podnik například firmu, kde se sice používají lean nástroje, ale kultura a myšlení lidí se nezměnily.


Jednotlivé oblasti štíhlosti v organizaci zachycuje obrázek 1, přičemž je důležité reflektovat současný dynamický rozvoj také v řadě jiných oblastí, které zatím nejsou součástí schématu. Příkladem může být nově vzniklý koncept „lean IT“, v rámci něhož vznikla řada technik usilujících o efektivní využívání informačních systémů s minimem nákladů a minimem dalších vstupů. Nicméně vraťme se k tématu logistiky.
Henry Ford byl v roce 1913 první, kdo definoval plýtvání v logistice. Tvrdil, že mít zásobu surovin nebo hotových výrobků přesahující požadavky je plýtvání, které jako každé jiné plýtvání má za následek zvýšení cen a nižší mzdy. Společnost Toyota pak ve svém produkčním systému Toyota Production System (TPS) rozvinula Fordův výrobní systém, dokonale zvládla procesy a využila všechny existující „zdravé a rozumné“ přístupy ve snaze dosáhnout maximální štíhlosti. Dodnes je tento systém považován za nepřekonaný a dokonale propracovaný výrobní systém, jehož otcem byl výrobní ředitel Toyoty Taiichi Ohno. Fordovy myšlenky převzal a ve svých závodech uplatnil i Tomáš Baťa, který se v roce 1919 vypravil do USA, aby se důkladně seznámil s organizací a řízením automobilových závodů Henryho Forda. Inspirován způsobem řízení Fordových závodů a vybaven vlastními zkušenostmi provedl rozsáhlou přestavbu a reorganizaci výroby v celé továrně. Baťa spojil důslednou racionalizaci a specializaci výrobních postupů, zejména zavedením proudové výroby, se snahou o eliminaci logistických činností.
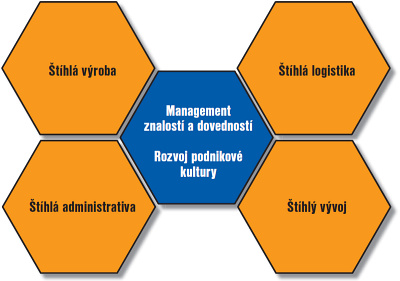
Obr. 1: Štíhlý podnik a jeho části
Podíváme-li se na problém z opačného hlediska, zjistíme, že výrobek se může vyskytovat pouze ve čtyřech stavech, kterými jsou doprava, skladováni, výroba a kontrola. Je zcela evidentní, že je to pouze stav výroby, který zajišťuje nárůst hodnoty, přičemž další tři z vyjmenovaných stavů se na tvorbě přidané hodnoty nepodílejí. V praxi je naprosto běžné, že většina procesů je tvořena z více jak 95 procent činnostmi, které nepřidávají hodnotu, a pouze pět procent a méně je tvořeno činnostmi přidávajícími hodnotu. Ke své vlastní škodě se většina firem chybně soustřeďuje právě na oněch zmíněných pět procent činností (procesů), které hodnotu přidávají, a snaží se prostřednictvím značných investic snižovat normy na operace a zvyšovat výrobní výkonnost technologií.
Štíhlá logistika hledá skutečné příležitosti a nalézá je právě v oněch činnostech, které hodnotu jako takovou nepřidávají, naopak pouze zvyšují náklady na realizaci výrobku či služby. Zde je možné dosáhnout zlepšení v řádu až několika desítek procentních bodů. V další části se zaměříme na způsob, jakým toho lze dosáhnout.
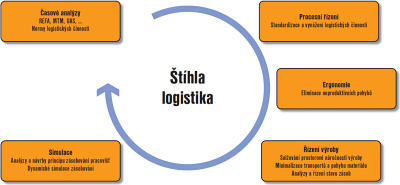
Obr. 2: Jak dosáhnout štíhlé logistiky
Časové analýzy
Výrobní procesy jsou v podniku obvykle středem zájmu. Jejich správné popsání, standardizování a znormování je pro výrobu klíčové, a právě z tohoto důvodu je jim věnována taková pozornost. U logistických činností to však neplatí bez výjimky. I když jsou tyto činnosti pro výrobu nezbytné, stále jsou v mnoha firmách zanedbávané, což je dáno především obtížnou standardizací a problematickým časovým určením.
Téměř všechny podnikatelské subjekty dnes plánují potřebné výrobní kapacity dle aktuálního stavu produkce. Vysvětleno na jednoduchém případě to může znamenat, že pro týdenní produkci patnácti set kusů výrobků na lince potřebujeme devět výrobních dělníků a další týden pro produkci osmi set kusů výrobků pouze pět výrobních dělníků. S tím ovšem souvisí i změna objemu zásobování, a tedy nižší nároky na logistické procesy. Dochází tedy také k ponížení potřebného stavu pracovníků v logistice? Pokud nikoli, měli bychom se zaměřit na časové analýzy logistických procesů.
Cílem časových analýz v oblasti štíhlé logistiky je standardizovat, jasně popsat a časově vymezit logistické procesy, neboť právě tyto jsou nutným základem pro důsledné kapacitní plánování. S využitím metod časové racionalizace jsme schopni jasně determinovat délku a účinnost jednotlivých logistických procesů, což nám následně umožní tyto logistické procesy kapacitně plánovat.
Hlavními přínosy jsou:
- standardizované logistické činnosti,
- jednoznačně určená časová náročnost jednotlivých logistických činností,
- podklady pro kapacitní plánování s vysokou vypovídací hodnotou,
- podklady pro efektivní odměňování pracovníků,
- identifikace ztrátových činností.
Procesní řízení
V rámci procesního řízení dochází primárně k důslednému zmapování všech procesů v podniku s cílem minimalizovat procesy nepřidávající hodnotu a tyto pak následně na dosažené minimální úrovni standardizovat. Pro mapování hodnotového toku je k dispozici analytický nástroj value stream mapping (VSM), který mapuje všechny procesy od vstupního materiálu až k hotovému výrobku. Výstupem VSM je ucelený pohled na hodnotový tok výrobku, který odhalí možné ztráty, úzká místa a důvody neefektivního toku v procesech na pracovišti nebo ve skladech. Hlavním cílem aplikace zmíněného nástroje je navrhnout budoucí „ideální“ stav bez plýtvání.
Po identifikaci procesů je nutná jejich standardizace, aby vlivem odlišného přístupu pracovníků nedocházelo ke zvýšenému plýtvání v důsledku nárůstu logistických procesů. Příkladem může být studie normování logistických procesů ve skladu jednoho z významných dodavatelů automobilového průmyslu. V rámci této studie bylo realizováno normování logistických činností (procesů) ve třísměnném provozu skladu, přičemž bylo zjištěno, že proces vyskladňování materiálu probíhal na každé směně jiným způsobem. To ovšem znamenalo, že byly na jeden logistický proces získány tři odlišné časy pro stanovení normy. Je tedy zcela evidentní, že dvě směny trvale plýtvaly.
Ergonomie
Ergonomie je v oblasti logistických procesů základním nástrojem pro odstranění plýtvání ve formě zbytečných pohybů na pracovištích. Jejím cílem je navrhnout uspořádání pracovního místa a souvisejících pracovišť takovým způsobem, aby veškeré pohyby byly realizovány co možná nejefektivněji. Řešení ergonomických úloh lze dle odborného přístupu k problematice rozdělit na dva základní typy úloh – ergonomie velkých celků a ergonomie při opakované výrobě drobných součástek.
Výroba nebo montáž drobných výrobků v opakované výrobě je hojně zastoupena v každém průmyslovém odvětví. Na první pohled se může zdát, že při tomto charakteru výroby se jedná o velice krátké a rychle opakované pohyby, u kterých jejich částečné zkrácení nebude přinášet velké efekty. Vyjděme z modelové situace montáže výrobků na jednom pracovišti v taktu šedesát sekund na kus. Na základě realizovaných ergonomických opatření (zkrácení pohybů při montáži) došlo k úspoře pěti sekund, a tedy zkrácení taktu na 55 sekund. Na první pohled se zdá úspora v řádu několika sekund jako zanedbatelná. Ovšem produkce za pracovní směnu byla v původní variantě 480 kusů a ve variantě po ergonomických úpravách 523 kusů. To představuje zvýšení produktivity pracoviště o celých devět procent.
Vytvořit optimální pracovní prostor či podmínky pro rozměrné produkty je již komplikovanější, jelikož dochází k postupnému střídání pracovníků na vyráběném produktu, ke kterému si vozí nářadí nebo mobilní pracoviště. Pomocí ergonomických nástrojů lze analyzovat pracovní polohy jednotlivých činností dokonce až s ohledem na fyzické proporce zaměstnance, a zajistit tak optimální podmínky pro vykonávání pracovních činností. Pojem optimální v tomto smyslu reprezentuje podmínky s minimem neproduktivních pohybů a bez rizika přetěžování pracovníků.
Řízení výroby
Spaghetti diagram (obr. 3) je jedním z hlavních a zároveň nejjednodušších nástrojů pro zachycení pohybu materiálu nebo pracovníka v předem definovaném časovém úseku, kterým může být například jeden den. Sledování pohybů je nezbytnou součástí zeštíhlování procesů. Jedná se o proces hledání zbytečných pohybů, odchodů, zbytečných transportů a manipulace se záměrem lépe organizovat layout pracoviště a minimalizovat logistické procesy včetně skladování.
Vytvoření spaghetti diagramu je poměrně jednoduchou záležitostí, ke které není potřeba žádný software. Vhodné je diagram zaznamenávat do layoutu budovy nebo její části, kdy jsou zachycovány pohyby pracovníka či manipulace s materiálem do obrázku. Následně je realizován rozbor ušlé vzdálenosti, možnosti zkrácení trasy, redukce zbytečných pohybů a přiblížení potřebného materiálu s cílem minimalizace všech logistických procesů.
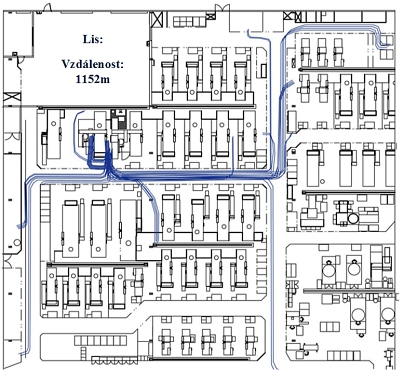
Obr. 3: Spaghetti diagram
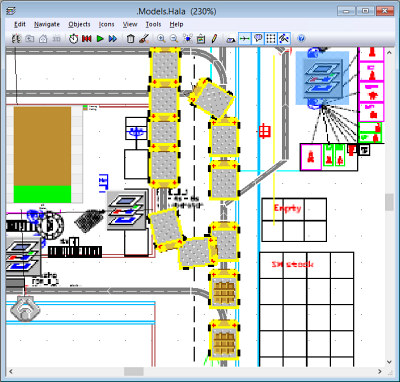
Obr. 4: Obrázek ilustruje situaci, ve které došlo ke kolapsu dopravního systému
z důvodu vzájemné blokace dvou různých AGV
Obrázek 3 v tomto konkrétním případě zachycuje pohyb pracovníka při přetypování stroje. To bylo realizováno tím způsobem, že byl od zahájení výměny nástroje na lisu zakreslován do layoutu haly pohyb seřizovače. Z výsledků je zcela patrné, že seřizovač v průběhu výměny minimálně šestkrát opustil pracoviště a tím značně prodloužil čas výměny nástroje a způsobil plýtvání jak vlastním časem, tak časem stroje. Pro potenciální použití je zajímavá skutečnost, že spaghetti diagramy mohou být využívány i v jiných než výrobních oblastech, přičemž se ukázaly být velmi užitečnými i při mapování procesů v administrativě.
Simulace
Simulace se v současné době stává neodmyslitelným nástrojem využívaným pro návrh, optimalizaci či provoz jakéhokoliv složitějšího systému. Trend customizace výrobků při současném snižování výrobních dávek klade značný důraz na správnou funkci logistických toků a zásobování materiálem, přičemž lze konstatovat, že simulace je v těchto případech nezbytností. Na druhé straně případná realizace simulačního modelu přináší celou řadu výhod od nezanedbatelných finančních úspor až po tržní konkurenční výhodu.
Počítačová simulace je metodou, která pomocí počítačového modelu logistického procesu umožňuje manažerům předvídat výrobu při změně podmínek a optimalizovat dopravní systém vzhledem k zadaným kritériím. Samotné řešení je založeno na jednoduchém principu, kdy je pomocí specializovaného simulačního nástroje vytvořen počítačový model, který se bude chovat stejně jako realita a na kterém se následně dělají pokusy, které odpovídají na otázky typu „co se stane, když“.
Příkladem pro simulační úlohu v oblasti logistických procesů může být přechod systému zásobování na Automatický logistický systém AGS. Tento přechod představuje změnu způsobu zásobování standardní manipulační technikou s obsluhou na zásobování automaticky řízenými vozíky bez obsluhy – AGV. Podstatné pro zadání úlohy v tomto případě je, že parametry vozíků s obsluhou jsou značně odlišné od parametrů vozíků bez obsluhy, a proto chování těchto dvou systémů bude do značné míry odlišné. Obrázek 4 ilustruje situaci, ve které došlo ke kolapsu dopravního systému z důvodu vzájemné blokace dvou různých AGV.
Michal Šimon, Antonín Miller
Ing. Antonín Miller je doktorandem na katedře průmyslového inženýrství a managementu Západočeské univerzity v Plzni. Ve své práci se zaměřuje na výrobní layout, digitální podnik a logistiku.


23.9. | PragVue 2025 |
23.9. | Virtuální konference Jak splnit nový zákon o kybernetické... |
25.9. | Cyber Attacks 2024 |
1.10. | Cyber Attacks 2025 |
21.10. | Bezpečnosť a dostupnosť dát 2025 |
Formulář pro přidání akce
13.8. | Webinář: Jak efektivně řídit obchodní aktivity ve firmě?... |
29.9. | The Massive IoT Conference |