- Přehledy IS
- APS (20)
- BPM - procesní řízení (23)
- Cloud computing (IaaS) (10)
- Cloud computing (SaaS) (32)
- CRM (52)
- DMS/ECM - správa dokumentů (20)
- EAM (17)
- Ekonomické systémy (68)
- ERP (75)
- HRM (28)
- ITSM (6)
- MES (34)
- Řízení výroby (36)
- WMS (29)
- Dodavatelé IT služeb a řešení
- Datová centra (25)
- Dodavatelé CAD/CAM/PLM/BIM... (41)
- Dodavatelé CRM (38)
- Dodavatelé DW-BI (50)
- Dodavatelé ERP (68)
- Informační bezpečnost (49)
- IT řešení pro logistiku (45)
- IT řešení pro stavebnictví (26)
- Řešení pro veřejný a státní sektor (27)


















![]() | Přihlaste se k odběru zpravodaje SystemNEWS na LinkedIn, který každý týden přináší výběr článků z oblasti podnikové informatiky | |
![]() | ||
Vytěžování výrobních dat pro zefektivnění výroby
Výrobní podniky v naší zemi kladou čím dál větší důraz na kvalitu a efektivitu. Týká se to veskrze všech procesů, které markantně ovlivňují jejich byznys. Zatímco před magickým rokem 2008, tedy počátkem všeobjímající paniky trhu prorůstající z finančních sfér napříč celou společností, kdy se v mnoha případech „nějak vyrábělo“, je dnes situace poněkud jiná.


Výhodu měly a mají podniky, které adoptovaly některou z manter, jako například TPS (Toyota Production System) či jiné „lean“ metodiky řízení. Častým problémem jsou ale chybějící nástroje, kterými lze zmíněné metodiky aplikovat přímo v praxi. Výsledkem této „díry“ jsou v lepším případě čísla, která vypadají víceméně dobře na papíře. V případě horším pak vypjaté situace na výrobních linkách, způsobené enormní snahou dohánět plán.
Produktem výroby jsou také klíčová data
Právě pro výrobní linky existuje řada řešení, která se pokouší pomoci se stavem věcí. Mezi silná očekávání, která jsou s takovými řešeními spojena, určitě patří vytvoření efektivního systému podpory řízení kvality, systému podpory optimalizace výrobních procesů a dalších. A efektivní systém znamená takový systém, který by měl umět zachytávat a vytěžovat něco, čemu se říká „machine data“. Právě v tom ohromném objemu, který se každou sekundu valí z výrobních a dalších zařízení v podniku. Jinými slovy hledáme něco, co nám pomůže začít se zajímat o velké bohatství, které v podobě oněch tryskajících, nepovšimnutých proudí ven z výroby a mizí v mlze zapomnění. Co ale konkrétně znamená to „něco“? Ukažme si na dvou reálných příkladech, proč jsou výše zmíněné podpůrné systémy nezbytné.
Příklad 1 – Jak skutečné jsou prostoje, které nám hlásí operátoři na linkách?
Představme si výrobní linku. Pro ty z vás, kteří v této oblasti nejsou úplně doma, představu zhmotněme jako dlouhý hnědý stůl. Po jeho delší straně stojí vedle sebe několik lidí – malířů. Tito malíři mají za úkol za určitý čas společně nabarvit dárkovou krabici (viz obrázek 1). První malíř tedy udělá svůj díl a posune krabici dalšímu. Všichni vědí, co mají dělat a téměř určitě dbají na to, aby se krabice líbila zákazníkům.
Pokud by vše fungovalo ideálně, měli bychom stoprocentně loajální zaměstnance. Takový dokonale loajální zaměstnanec netrpí žádnou jinou fyzickou či mentální potřebou než malovat krabice. V takovém případě bychom nepotřebovali žádný kontrolní systém, a jestli to tak u vás funguje, nemusíte už číst dále. Jenže ve skutečnosti tomu tak v drtivé většině případů není, a tak se čas od času stane, že si někdo odskočí na záchod, jiný na cigaretu, jiný má „den blbec“. No a někdo třeba nechodí do práce, ale do zaměstnání a polovinu pracovní doby jednoduše prolelkuje.
K výkonnosti si, přes výše zmíněné okolnosti, pomáháme lepšími definicemi operací. Každý malíř u našeho hnědého stolu má daný určitý čas, za který má splnit svou část práce. Když tyto časy sečteme, vyjde nám celkový čas, za který bude krabice namalována. Ve výrobním žargonu se tomuto času říká „cycle time“.
Nyní si zkuste představit místo hnědého stolu s malíři poloautomatizovanou linku (viz obrázek 2). Lidé, v tomto případě operátoři, místo štětce a barvy řídí každý svou část procesu sestavování výrobku – nazveme ho třeba Udělátor. Ten se skládá z mnoha integrovaných obvodů, z nichž každý je instalován jedním z operátorů v pořadí podobném našim malířům.
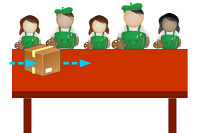
Obr. 2
Je zřejmé, že cycle time (tedy čas průchodu výrobní linkou nebo malířským stolem) bude s každým Udělátorem různý. S tím jsme smířeni, pokud výkyvy nejsou příliš velké. V případě, že velké jsou, chceme zjistit, čím je to. Co se v průběhu pracovní doby stalo, děje (nebo bude dít), že nestačíme plnit plán? Jak poznáme, jestli za to mohou prodlevy způsobené svévolí operátora nebo objektivní příčina – třeba neoptimálním programem PLC? Vodítko se pokusme nalézt v dalším obvyklém příkladu z praxe.
Příklad 2 – Identifikace objektivních příčin nárůstu cycle time
Vraťme se na chvíli k obrázku malířů krabic a hnědému stolu. Co by bylo onou objektivní příčinou srovnatelnou s neoptimálním programem PLC? Mohl by to být například špatný odstín barvy, kterou malíř vyfasoval. Nebo příliš úzký štětec. Možná je to i málo místa u stolu? Můžeme se jít přesvědčit, zeptat se každého malíře.
Analogicky, pokud chceme znát příčinu dlouhého cycle time, můžeme se zeptat stroje. Narozdíl od příkladu s malíři, ale onen stůl představují desítky nebo i stovky výrobních linek. V našem případě tedy nutně potřebujeme sbírat data jinak než ústně (pomineme-li základní a doposud opomíjenou nepříjemnost, že výrobní stroje za běžných okolností nemluví). Je tedy nasnadě zkusit to například automatizovaně z PLC. PLC může posílat stavy jednotlivých kroků procesu výroby, z nichž vhodnou interpretací dostaneme informace a náhled o tom, jak daná linka funguje. Podobně můžeme využít například PC na linkách, jehož prostřednictvím (a za pomoci konkrétního software) operátoři potvrzují svůj krok na lince (podobně by si mohl náš malíř udělat čárku za každé obarvení na papírek). V neposlední řadě můžeme využít také testery na koncích linek (obrázek 3).
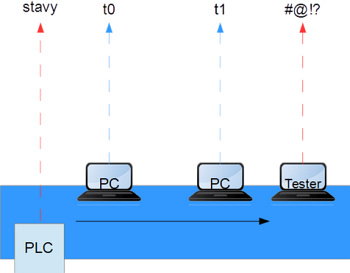
Obr. 3
Rozuzlení – poznatky a hodnoty plynoucí z našich dvou příkladů?
Situace, které vyžadují naši zvýšenou pozornost, nás mohou potkat při mnoha příležitostech. Těmi mohou být zavádění nového produktu nebo změna výrobního procesu. Spouštěčem neobvyklosti může být i nepřímý, například vysoká fluktuace zaměstnanců (a neustálé chyby způsobené nezkušeností nových operátorů). V každém případě chceme dosahovat optimální výroby, chceme vědět, co je příčinou neshod, zanalyzovat možnosti zlepšení. Chceme vědět, že vyrábíme kvalitní výrobky a ne problémové situace.
A protože toto je to pravé místo v článku pro dobrou zprávu, že existují elegantní řešení, která pomohou zjistit příčiny nekvality a návazně i příčiny výkyvů cycle time.
Nástroje na analýzu (nejen) výrobních dat v reálném čase
Ke zpracování výstupů z PLC, výrobních PC na lince a např. software pro záznam výrobního procesu je vhodné použít robustní nástroj, který umožňuje dávkově nebo v reálném čase tyto výstupy přijmout, uložit, zanalyzovat a poskytnou okamžitou odezvu. Předpokladem úspěchu při zpracování strojových dat je, aby zvolené řešení mělo několik klíčových vlastností:
- Umí pracovat s obrovským objemem vstupních dat v reálném čase.
- Umí v reálném čase tato data korelovat (vytvářet mezi nimi souvislosti).
- Umí v reálném čase tato data analyzovat.
- Umí v reálném čase tato data vizualizovat (prostřednictvím nástěnek, reportů, výstrah).
Díky takovému řešení bude možné:
- sbírat průběžně data z desítek nebo stovek výrobních linek (a provádět nad daty např. analýzu podporující statistickou regulaci procesů – SPC),
- díky zobrazeným souvislostem najít základní příčiny problémových situací (např. lze namodelovat Ishikawa diagram),
- díky ukládání historických dat mohu sledovat trendy a poskytovat podklady pro finanční oddělení a kvalitáře,
- jsem schopen sledovat dopady inovací, reinženýrinku apod., např. dle metodiky PPAP, a podporovat tak udržení kvalitativních certifikátů (např. Ford Q1, ISO/TS 16949 apod.),
- jsem schopen podporovat plánování další kapacity/linek na základě sběru výkonových dat,
- mohu velmi názorně a na vyžádání poskytovat reporty vedení, zákazníkům nebo jejich zástupcům (např. STA).
Pokud se ale zpět zaměříme z obecných přínosů na konkrétní, svázané s našimi dvěma příklady, pak mi nasazení zmíněného systému umožní:
- sběr dat z PLC sledovaných linek
- sběr dat z PC a testerů daných linek (buď přímo ze zařízení nebo z datových exportů těchto zařízení)
- určit příčinu prodlev v cycle time (a v případě úmyslu neproplatit tento „idle time“ operátorům, kteří nedbalostí nebo záměrně brzdí výrobní proces)
- argumentovat během výrobních porad pravou a základní příčinou diskrepancí v kvalitě a čase (dostávám nástroj, který mi umožní ukázat a prezentovat)
- predikovat vývoj událostí na výrobních linkách
- rozvoj pro další případy užití (jako je sběr dat z jiných zařízení, včetně analogových – např. lisů, čidel z výrobních pásů, nádob, zásobníků apod.)
- technologii, jejímž základem je zpracování velkých datových objemů („big data“) a je připravena pro IoT (Internet věcí – ve výrobní sféře to znamená sběr nejrůznějších veličin z různých typů zdrojů/čidel)
Jak může vypadat jeden z mnoha modelů využití systému zakomponovaný do našich dvou příkladů ukazuje obrázek 4.
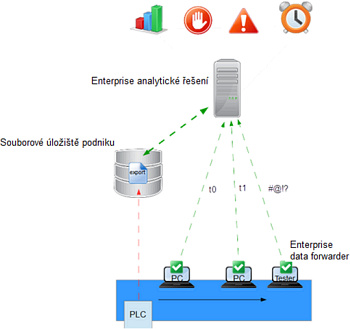
Obr. 4
![]() |
Kamil Brzák Autor článku pracuje na pozici projektového manažera a konzultanta big data řešení ve společnosti Trask solutions a.s. |


23.9. | PragVue 2025 |
23.9. | Virtuální konference Jak splnit nový zákon o kybernetické... |
25.9. | Cyber Attacks 2024 |
1.10. | Cyber Attacks 2025 |
21.10. | Bezpečnosť a dostupnosť dát 2025 |
Formulář pro přidání akce
13.8. | Webinář: Jak efektivně řídit obchodní aktivity ve firmě?... |
29.9. | The Massive IoT Conference |