- Přehledy IS
- APS (21)
- BPM - procesní řízení (23)
- Cloud computing (IaaS) (9)
- Cloud computing (SaaS) (29)
- CRM (49)
- DMS/ECM - správa dokumentů (19)
- EAM (16)
- Ekonomické systémy (68)
- ERP (87)
- HRM (27)
- ITSM (6)
- MES (32)
- Řízení výroby (47)
- WMS (28)
- Dodavatelé IT služeb a řešení
- Datová centra (25)
- Dodavatelé CAD/CAM/PLM/BIM... (40)
- Dodavatelé CRM (36)
- Dodavatelé DW-BI (50)
- Dodavatelé ERP (80)
- Informační bezpečnost (42)
- IT řešení pro logistiku (46)
- IT řešení pro stavebnictví (25)
- Řešení pro veřejný a státní sektor (26)
Partneři sekce
Tematické sekce


















Branžové sekce
![]() | Přihlaste se k odběru zpravodaje SystemNEWS na LinkedIn, který každý týden přináší výběr článků z oblasti podnikové informatiky | |
![]() | ||
Partneři webu
IT SYSTEMS 7-8/2006 , Plánování a řízení výroby
TOC – nový nástroj řízení nejen výroby
Ing. Josef Čipera, MBA
Konkurenční prostředí, ve kterém se výrobní firmy snaží uspět, vytváří stále větší tlak na efektivní plánování a řízení výroby. Bez zkracování průběžné doby, bezvadného plnění termínů dodávek, požadované kvality výrobků, okamžité reakce na změny atd. se šance uspět výrazně snižují. A protože současné systémy řízení obvykle potřebnou podporu nemají, nezbývá než hledat nové cesty. Jednou z nich je řízení podle úzkých míst, dnes již známé jako TOC (theory of constraints). V následujícím textu jsou poněkud netradičně hodnoceny současné možnosti plánování a řízení výroby, provedeno jejich srovnání s novým způsobem řízení včetně zajištění informační podpory.
Rekapitulace současného stavu
Firmy mají dnes na vybranou ze tří základních systémů řízení výroby: MRP (II), APS a JIT. Mimo jiné je možné hodnotit tyto systémy podle:
Nové možnosti řízení
Dnes již existuje zcela nové řešení, které beze zbytku splňuje výše uvedená kritéria. Vyhovuje nejen pro diskrétní strojírenskou výrobu, ale je možné je využít i pro specializované typy výrob, jako jsou lisovny, nástrojárny, kovovýroby a řada dalších.
Obr. 1: Plánování a řízení výroby dle TOC
Druhou veličinou je buffer – časový nárazník. Jak vyplývá z názvu, nejedná se o fyzickou zásobu například polotovarů, ale o předem definovaný časový úsek. Ten garantuje, že se zakázka dostane na úzké místo včas tak, aby „nevyhladovělo“, respektive aby byl splněn termín dodání. Výpočet velikosti bufferu je jednoduchý. Díky tomu, že se operace plánují za sebou bez významných čekacích časů, je možné zkrátit standardní průběžnou dobu na polovinu. Ta se ještě rozdělí na tři části v souladu s principem semaforu. Základním předpokladem je, že se jednotlivé operace provedou s rezervou za dvě třetiny času. Třetí třetina pak slouží jako časová ochrana pro případ, že dojde k poruše, bude chybět materiál nebo obsluha atd. Na obr. 2 je znázorněn buffer včetně barevného vyznačení jeho částí, číslice znamenají například jednotlivé dny.
Obr. 2: Rozdělení bufferu do tří oblastí
Poslední veličinou je rope – lano – v závislosti na pořadí a délce průběžné doby zakázky je zřejmé, kdy má být uvolněn materiál do výroby.
Pro řízení výroby se využívá nesmírně jednoduchý, ale přitom velice účinný nástroj zvaný buffer management. Tento systém umožňuje koncentrovat úsilí pouze na několik ohrožených zakázek, které jsou ve zpoždění. Místo sledování, co je na každé zakázce již hotové a co ještě zbývá, se využívá stavu bufferu, který zároveň vyjadřuje stav zakázky. To umožňuje lépe koncentrovat úsilí (včetně doby trvání operativních porad) tam, kde je ho nejvíce potřeba. Stav bufferu = (celková délka bufferu – čerpání bufferu dodnes) / celková délka bufferu.
Obr. 3: Stav zakázek (bufferů)
Pro řízení výroby je využit stejně jako v předchozím případě buffer management. Zatímco u jednoduchých výrob je délka bufferu rovna délce průběžné doby, v tomto případě se buffer připojuje za vytvořený plán. Jeho velikost je možné zvolit například jako procento z průběžné doby zaplánované zakázky, nebo absolutní hodnotou apod. Také zde se buffer rozdělí na tři části a využívá principu semaforu. Celkovou průběžnou dobu neprodlužuje, protože plán je vytvořen na základě čistých technologických časů. Pokud se zakázka zpožďuje, dochází k tzv. penetraci do bufferu a včasnému varování podobně jako u jednoduchých výrob. Na obr. 4 je zakázka je zaplánována například na prvních šest dní, zbývající tři dny tvoří buffer.
Uvolnění materiálu do výroby, rope neboli lano, je stanoveno první prováděnou operací.
Obr. 4 Buffer pro složitější výrobu
Druhou možnost představují různé nadstavby fungující nad MRP systémy, u nichž je plánovací srdce MRP nahrazeno DBR. Využívá se například Excel, nebo specializované klient/server aplikace. Podpora TOC v oblasti plánování a řízení výroby DBR pak bývá doplněna další funkcionalitou, jako je průtokové účetnictví TA (throughput accounting), projektové řízení na bázi kritického řetězu CCPM (critical chain project management), průtokové měření výkonnosti a další.


Rekapitulace současného stavu
Firmy mají dnes na vybranou ze tří základních systémů řízení výroby: MRP (II), APS a JIT. Mimo jiné je možné hodnotit tyto systémy podle:
- schopnosti vytvořit skutečně reálný, a tudíž splnitelný plán,
- robustnosti, neboli odolnosti vůči rušivým vlivům, jako jsou poruchy strojů, vyrobené zmetky, nedostupnost materiálu, lidí atd.,
- možnosti simulovat různé výrobní varianty, nabídky apod.
- MRP (II) – stále tvoří základ celopodnikových ERP systémů. Hodí se především pro sériovou výrobu, umožňuje tzv. zhromadňování výrobních zakázek atd. Ad 1) nevytvoří reálný plán, protože plánuje do neomezených kapacit, potřeba materiálu je naplánována chybně. Ad 2) ochrana termínu zakázky není, narůstají náklady kvůli „hašení“ problémů. Ad 3) simulace na nereálném plánu ztrácí smysl, případný přepočet plánu by byl stejně časově neúnosný. Obezličkou je využití tzv. čisté změny, kdy se nový požadavek „přilepí“na stávající plán.
- APS, systémy pokročilého plánování – ad 1) vytvoří reálný plán do omezených kapacit na základě nastavených parametrů, například maximálního využití kapacit. Ad 2) vše je naplánováno „na minutu“ přesně, termín zakázky však ochráněn není. Ad 3) simulace je možná. V úvahu je však třeba vzít pořizovací cenu, která nebývá zrovna nízká.
- JIT – známý díky Toyotě, je vhodný pro montážní výrobu (např. automobilů). Ad 1) plán je reálný, ad 2) ani v tomto případě termín zakázky ochráněn není, pokud se vyskytne problém, zastavuje se výroba, ad 3) simulace je možná.
Nové možnosti řízení
Dnes již existuje zcela nové řešení, které beze zbytku splňuje výše uvedená kritéria. Vyhovuje nejen pro diskrétní strojírenskou výrobu, ale je možné je využít i pro specializované typy výrob, jako jsou lisovny, nástrojárny, kovovýroby a řada dalších.
- TOC, řízení podle úzkých míst – ad 1) vytvoří reálný plán, protože plánuje do omezených kapacit, potřeba materiálu odpovídá potřebě v čase. Ad 2) obsahuje tzv. časové nárazníky, které „pohlcují“ nepředvídané události a tím chrání termín splnění zakázky. Ad 3) velice snadno a rychle je možné simulovat varianty plánu, nové nabídky apod.
Synchronizovaná výroba – DBR (drum-buffer-rope)
Plánování pomocí tohoto TOC nástroje je velice jednoduché a intuitivní. Na rozdíl od současných plánovacích systémů, které neustále bilancují kapacity a požadavky, DBR zajišťuje plynulý tok výrobou. Prvotním zájmem tak paradoxně není snaha o maximální vytížení jednotlivých zdrojů, ale o co největší „průtok“. Díky tomuto způsobu řízení je možné zlepšit plnění termínů dodání, významně zkrátit průběžnou dobu, snížit náklady na „hašení“ problémů, ale i zásoby včetně rozpracované výroby atd. Jak potvrzuje praxe, kapacitní možnosti firem jsou obvykle (mnohem) větší než požadavky, které mají pokrýt. Je však potřeba odlišit zdroje s dočasným nedostatkem kapacity, a skutečné(á) omezení. Právě to je největším kamenem úrazu těch, kdo se začali TOC, respektive DBR, zabývat. V případě, že firma má dostatečné kapacity, podřizuje se plán termínu dokončení zakázky. Pokud existuje fyzické omezení uvnitř firmy, je nutné vytvořit plán tak, aby byl nejen splněn termín zakázky, ale i co nejlépe využito omezení.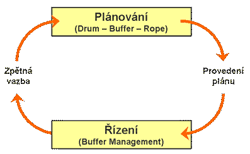
Obr. 1: Plánování a řízení výroby dle TOC
Jednoduché typy výrob
Tzv. manuální implementace DBR je zvláště vhodná pro malé a střední firmy. Plán se v tomto případě vytváří ručně, případně za pomoci informační podpory, a to pouze na konkrétní, úzký zdroj. Výchozím předpokladem je, že ostatní zdroje mají dostatečnou kapacitu vzhledem k předpokládané zátěži. Drum – bubeník – pak určuje rytmus celé výroby, kterým je pořadí provádění jednotlivých zakázek. Práce na ostatních pracovištích se podřizují úzkému místu. Cílem je co nejlépe využít úzký zdroj, protože každá minuta na něm ztracená, ať již z jakéhokoliv důvodu, je nenávratně pryč.Druhou veličinou je buffer – časový nárazník. Jak vyplývá z názvu, nejedná se o fyzickou zásobu například polotovarů, ale o předem definovaný časový úsek. Ten garantuje, že se zakázka dostane na úzké místo včas tak, aby „nevyhladovělo“, respektive aby byl splněn termín dodání. Výpočet velikosti bufferu je jednoduchý. Díky tomu, že se operace plánují za sebou bez významných čekacích časů, je možné zkrátit standardní průběžnou dobu na polovinu. Ta se ještě rozdělí na tři části v souladu s principem semaforu. Základním předpokladem je, že se jednotlivé operace provedou s rezervou za dvě třetiny času. Třetí třetina pak slouží jako časová ochrana pro případ, že dojde k poruše, bude chybět materiál nebo obsluha atd. Na obr. 2 je znázorněn buffer včetně barevného vyznačení jeho částí, číslice znamenají například jednotlivé dny.
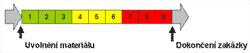
Obr. 2: Rozdělení bufferu do tří oblastí
Poslední veličinou je rope – lano – v závislosti na pořadí a délce průběžné doby zakázky je zřejmé, kdy má být uvolněn materiál do výroby.
Pro řízení výroby se využívá nesmírně jednoduchý, ale přitom velice účinný nástroj zvaný buffer management. Tento systém umožňuje koncentrovat úsilí pouze na několik ohrožených zakázek, které jsou ve zpoždění. Místo sledování, co je na každé zakázce již hotové a co ještě zbývá, se využívá stavu bufferu, který zároveň vyjadřuje stav zakázky. To umožňuje lépe koncentrovat úsilí (včetně doby trvání operativních porad) tam, kde je ho nejvíce potřeba. Stav bufferu = (celková délka bufferu – čerpání bufferu dodnes) / celková délka bufferu.
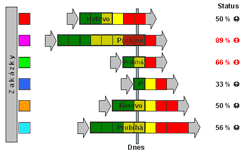
Obr. 3: Stav zakázek (bufferů)
Složitější výroby
Řízení složitějších výrob je prakticky nemyslitelné bez softwarové podpory. Algoritmy výpočtu obvykle zahrnují propočet kapacitního vytížení nejen úzkého místa, ale i ostatních firemních zdrojů. Zaplánování je prováděno zpětně, tj. od termínu dodání, a to do omezených kapacit. Pokud se vyskytne dočasné přetížení zdroje, plánovací nástroj rozhrne požadavky směrem dopředu do nejbližšího „údolí“. Není tak třeba ihned, kdy není k dispozici dočasná kapacita zdroje, řešit problém přidáním přesčasů nebo kooperacemi a tím zvyšovat náklady. Pokud si systém se zátěží neporadí, vyhrne požadavky až na první den. Plánování je interaktivní, tj. snahou není optimalizovat plán podle jednou nastavených podmínek. Na rozdíl od systémů APS, kde plánování probíhá v „černé skříňce“, v tomto případě rozhoduje o tom, co dál, člověk. Kromě zpožděných zakázek má například k dispozici seznam přetížených pracovišť, setříděných podle toho, jak ohrožují splnění termínů zakázek. Operativně může do plánu přidat přesčasy, další směny, přehodit operaci na jiné pracoviště, zajistit kooperaci atd. Provedená opatření pak může okamžitě nasimulovat včetně dopadu do firemních financí. Plán je počítán v paměti RAM, nová varianta je tak k dispozici během několika desítek vteřin. Také v tomto případě drum, bubeník, určuje rytmus celé výroby, kdy kromě stanoveného pořadí prováděných zakázek bývá k dispozici tzv. lhůtový plán, neboli fronta práce na každé pracoviště a den. Mistři tak dostanou reálný dílenský plán, jejich úkolem je zajistit jeho plnění.Pro řízení výroby je využit stejně jako v předchozím případě buffer management. Zatímco u jednoduchých výrob je délka bufferu rovna délce průběžné doby, v tomto případě se buffer připojuje za vytvořený plán. Jeho velikost je možné zvolit například jako procento z průběžné doby zaplánované zakázky, nebo absolutní hodnotou apod. Také zde se buffer rozdělí na tři části a využívá principu semaforu. Celkovou průběžnou dobu neprodlužuje, protože plán je vytvořen na základě čistých technologických časů. Pokud se zakázka zpožďuje, dochází k tzv. penetraci do bufferu a včasnému varování podobně jako u jednoduchých výrob. Na obr. 4 je zakázka je zaplánována například na prvních šest dní, zbývající tři dny tvoří buffer.
Uvolnění materiálu do výroby, rope neboli lano, je stanoveno první prováděnou operací.
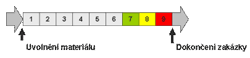
Obr. 4 Buffer pro složitější výrobu
Informační podpora
Využití informační podpory pro plánování a řízení výroby podle TOC může představovat skutečnou konkurenční výhodu jak pro implementační firmy, tak především pro jejich zákazníky. Stávající informační systémy však potřebnou funkcionalitou disponují spíše výjimečně. Jednou z možností je požadovat její doplnění od dodavatelů, kteří tak dokonce mohou do určité míry „vylepšit“ své MRP systémy, a to nejen v oblasti plánování, ale především řízení výroby.Druhou možnost představují různé nadstavby fungující nad MRP systémy, u nichž je plánovací srdce MRP nahrazeno DBR. Využívá se například Excel, nebo specializované klient/server aplikace. Podpora TOC v oblasti plánování a řízení výroby DBR pak bývá doplněna další funkcionalitou, jako je průtokové účetnictví TA (throughput accounting), projektové řízení na bázi kritického řetězu CCPM (critical chain project management), průtokové měření výkonnosti a další.
TOC je výzvou
Firmy často vkládají velké naděje do informační podpory. Velice dobře totiž vědí, že jejich dodavatelé jsou na špici v uplatňování nových metod řízení. Samotné softwarové společnosti jsou navíc tlačeny ke snižování cen licencí a tak vyhledávají služby s vyšší přidanou hodnotou. TOC je tak pro všechny velkou výzvou, protože nabízí komplexní řešení. Umožňuje získat doživotní zákazníky, protože jeho implementace je spíše procesem (neustálého zlepšování). Vytěžit maximum z TOC znamená změnit stávající vzorce chování, nastavená pravidla řízení, to, čemu lidé věří. V tom zároveň spočívá největší obtíž jeho zavedení, bezprostředně totiž ovlivňuje změnu podnikové kultury.Chcete získat časopis IT Systems s tímto a mnoha dalšími články z oblasti informačních systémů a řízení podnikové informatiky? Objednejte si předplatné nebo konkrétní vydání časopisu IT Systems z našeho archivu.


![]() ![]() | ||||||
Po | Út | St | Čt | Pá | So | Ne |
1 | 2 | 3 | 4 | 5 | 6 | 7 |
8 | 9 | 10 | 11 | 12 | 13 | 14 |
15 | 16 | 17 | 18 | 19 | 20 | 21 |
22 | 23 | 24 | 25 | 26 | 27 | 28 |
29 | 30 | 1 | 2 | 3 | 4 | 5 |
6 | 7 | 8 | 9 | 10 | 11 | 12 |
IT Systems podporuje
13.5. | Konference ISSS 2024 |
15.5. | Digitalizácia procesov vo výrobe a obchode |
15.5. | Kontajnery v praxi 2024 - Bratislava |
22.5. | Cloud Computing Conference 2024 |
Formulář pro přidání akce
Další vybrané akce
16.5. | Virtuální konference "Security as a Service"... |
22.5. | DYTRON EXPERIENCE FORUM 2024 |
13.6. | Konference ABIA CZ 2024: Inovacemi k růstu |