- Přehledy IS
- APS (22)
- BPM - procesní řízení (23)
- Cloud computing (IaaS) (9)
- Cloud computing (SaaS) (29)
- CRM (49)
- DMS/ECM - správa dokumentů (19)
- EAM (16)
- Ekonomické systémy (68)
- ERP (87)
- HRM (27)
- ITSM (6)
- MES (32)
- Řízení výroby (52)
- WMS (28)
- Dodavatelé IT služeb a řešení
- Datová centra (25)
- Dodavatelé CAD/CAM/PLM/BIM... (40)
- Dodavatelé CRM (36)
- Dodavatelé DW-BI (50)
- Dodavatelé ERP (80)
- Informační bezpečnost (42)
- IT řešení pro logistiku (46)
- IT řešení pro stavebnictví (25)
- Řešení pro veřejný a státní sektor (26)


















![]() | Přihlaste se k odběru zpravodaje SystemNEWS na LinkedIn, který každý týden přináší výběr článků z oblasti podnikové informatiky | |
![]() | ||
Štíhlé principy a procesně orientovaná výroba
Výrobní podniky už více jak padesát let investují nemalé peníze a čas do zavádění principů štíhlé výroby. Ty dal světu automobilový gigant Toyota, a je proto přirozené, že jsou ušity na míru procesům diskrétní výroby. Přesto si je mohou osvojit i procesně orientované podniky.


Štíhlá výroba neboli Toyota Production System (TPS), je dnes vnímána jako koncept, filozofie, praxe a soubor nástrojů v jednom. Její podstatou je zaměření na maximalizaci kvality, minimalizaci zbytečných výrobních kroků a zvyšování hodnoty produktu tím, že budeme dodávat přesně to, co zákazníci požadují, navíc ve správný čas. Proč bychom tyto principy nemohli aplikovat na procesně orientované výroby? I tam je přece zájem snižovat náklady, zvyšovat kvalitu a spokojenost zákazníka. Mnoho koncepčních nástrojů, které se vyvinuly z TPS, mohou být v prostředí procesní výroby využity. Podívejme se nyní na dva základní pilíře TPS a osm nástrojů, které mohou pomoci procesně orientovaným podnikům stát se „štíhlejšími“.
Pilíře štíhlého řízení
Koncept štíhlého řízení stojí na dvou základních principech, a to just in time a jidoka. Just in time je přístup k výrobě, který klade důraz na výrobu přesně toho, co zákazník chce, v přesně určeném čase, množství a kvalitě. Jidoka je japonský termín pro vynikající kvalitu. TPS chápe kvalitu jako primární faktor úspěchu a také všechny nástroje typické pro zavádění štíhlých principů se na zvyšování kvality produktů a procesů zaměřují. Navíc existuje několik fundamentálních zásad, které jsou se štíhlým řízením úzce svázány. Jsou jimi pojmy jako nejlepší kvalita, nejnižší náklady, nejkratší možný čas dodání a minimalizace plýtvání během produkčního procesu. Aby se tedy podnik mohl honosit přízviskem „štíhlý“, musí dodávat výrobky nejvyšší kvality a současně udržovat kvalitu procesů a co možná nejkratší realizační lhůty. Dalším důležitým principem lean (štíhlého řízení) je minimalizace plýtvání. Plýtvání je definováno jako jakýkoliv zdroj, který není adekvátně využíván. Mluvíme-li o zdrojích, automaticky se nám vybaví materiál, nicméně optikou lean považujeme za zdroje, jejichž využití je nutné optimalizovat, také čas, úsilí a samozřejmě zaměstnance. Proto je důležité se zaměřit také na analýzu využití zaměstnanců a času, aby bylo možné optimalizovat výkony a redukovat plýtvání. Přirozeně není snadné dosáhnout takto vysoce stanovených standardů. Aby jich organizace docílily, byla z TPS vyvinuta série konceptuálních nástrojů, z nichž mnohé můžeme aplikovat v prostředí procesní výroby. V následujícím textu si přiblížíme osm z nich.
Analýza hodnotového řetězce (value stream mapping)
VSM je základní technika štíhlého řízení. Používá se pro analýzu všech kroků ve výrobním procesu zahrnující toky materiálu, čas trvání každého kroku a identifikaci čekací doby mezi navazujícími aktivitami. Zahrnutí materiálových toků a času trvání činí z této techniky více než pouhou procesní mapu. Analýza hodnotového řetězce umožňuje identifikovat a eliminovat plýtvání.
Kaizen
Kaizen je japonský termín pro trvalé zlepšování. Je to kontinuální hledání příležitostí pro zlepšení v každé části procesu. Tuto filozofii by si měla osvojit každá úroveň organizace a aplikovat ji na všechny úlohy. Neustálé hledání cest, jak dělat věci efektivněji a precizněji pak vede k minimalizaci plýtvání a zvyšování hodnoty.
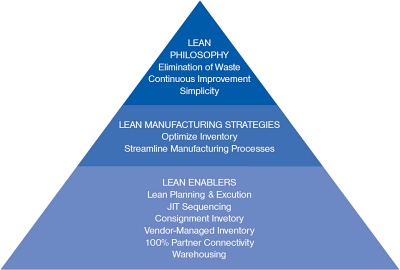
5S
Termín 5S označuje pět základních pravidel – rozděl (sort), uspořádej (straighten), ukliď (shine, systematic cleaning), standardizuj (standardise) a dodržuj (sustain). Těchto pět kroků popisuje, jak organizovat pracovní prostor. Proces rozdělení zahrnuje oddělení potřebných věcí od nepotřebných a odstranění nepořádku. Aby se minimalizoval čas hledání nástrojů a zároveň se zajistil snadný přístup k nim, je třeba věci a nástroje správně uspořádat. Další krok spočívá v uchovávání pracovního místa uklizeného a čistého, což zároveň přispívá k zachování funkčnosti věcí. Také se tím odstraňuje hromadění nepořádku a materiálu, které by mohlo způsobovat poškození produkce nebo vybavení pracovního místa. Standardizace zahrnují osvojení předchozích tří kroků tak, aby se z nich stala rutina. „Dodržuj“ je poslední ze zásad 5S a spočívá v udržování uvedených postupů pro každou operaci a část výroby.
Jidoka a TPM
Jak už jsme uvedli dříve, základem jidoky je úsilí o absolutní kvalitu. Tato filozofie tvoří v kombinaci s metodou totálně produktivní údržby (total productive maintenance) velmi cenný nástroj, který pomáhá organizacím na cestě za „štíhlostí“ neustále zvyšovat kvalitu. Podstata jidoky se jeví poměrně prostě. Jakmile je někde ve výrobě zjištěn problém s kvalitou, všechny aktivity se zastaví do té doby, dokud není vyřešen. Cílem je, aby se problémy řešily v místě jejich vzniku a nepostupovaly do následujících procesů. Dodržování této zásady je věcí každého zaměstnance.
TPM, někdy též označovaný jako autonomní údržba, je proces zlepšování způsobů, jakým jsou technologie využívány a udržovány. Pomáhá eliminovat problémy, zajišťovat adekvátní údržbu strojů pomocí striktních plánů údržby a průběžného vzdělávání zaměstnanců. S těmito principy by se měli ztotožnit všichni zaměstnanci, pro které by měly být motivačním prvkem ve snaze o „dokonalost“.
SMED
Další nástroj se skrývá pod zkratkou SMED, tedy single minute exchange of dies, což bychom mohli volně přeložit jako jediná minuta pro změnu nástroje. Jedná se o proces minimalizace doby, která je potřebná pro přestavení (seřízení) výrobního procesu z produkce jednoho produktu na druhý (changeover). I tento nástroj lze snadno uplatnit v procesně výrobních operacích. Jde o analýzu všech kroků, které je třeba učinit při seřízení linky a její přípravě na další odlišnou výrobní dávku. Podle SMED by mělo být v tomto procesu minimalizován čas a potřebný materiál. Ať už nastavujete cokoliv, tiskařský stroj nebo stáčecí linku, analýza a optimalizace seřízení strojů je tou správnou cestou ke štíhlé výrobě.
Pět proč
Víte, proč můžeme děti považovat za oddané stoupence štíhlých principů? Protože si skvěle osvojili další koncept štíhlé výroby, a to 5 proč. Tato metodika je postavena na neustálém kladení otázek a směle může být aplikována ve všech oborech, a vlastně na cokoliv v běžném životě. Kladení otázek je jednoduchá metoda vedoucí k porozumění problémům, jejich řešení a eliminování. Kladení otázek vede k poznání, jak věci fungují, a nalezení potenciální nápravy problému. Stejně jako u jidoky by všichni zaměstnanci měli být pobízeni, aby tento princip přijali a používali. Pokud uvidíte něco, čemu nerozumíte, zeptejte se proč.
Heijunka
Heijunka je prostředek dosažení stability. Tento japonský termín lze přeložit jako vyrovnávání nebo „vyhlazování“ výroby. Může zahrnovat vyrovnávání zátěže produkčních linek, synchronizaci produkčních běhů v závislosti na konkrétních atributech produktů a procesů apod. Nastavení navazujících akcí a produkčních běhů na základě velikosti, barvy, chuti a dalších charakteristik může minimalizovat časy potřebné k seřízení strojů mezi jednotlivými výrobními dávkami, eliminovat narušení procesu výroby a plýtvání a zároveň maximalizovat efektivitu. Například operace spojené s produkcí barev mohou být efektivnější, pokud vyrábíme barvy od světlých po tmavší, čímž minimalizujeme potřebu umývání vybavení mezi dvěma barvami.
Kanban
Poslední „štíhlý“ nástroj, který může být aplikován do prostředí procesních oborů je kanban. Kanban je proces vizuálního signalizování toho, co je potřeba vyrobit pro vykrytí zákazníkových objednávek. Kanban je proces, ve kterém se používají nástroje jako informační cedule nebo plánovací tabule, které upozorňují na to, co, kde, kdy má být vyrobeno a v jakém množství. Použití kanbanů (cedulí) zdůrazňuje v systému výroby princip tahu poptávkou v závislosti na tom, kdy chce mít zákazník produkt dodán. Samotný proces stojí na použití tzv. kanbanových karet. Kanbanová karta reprezentuje zprávu signalizující předcházejícímu výrobnímu stupni, že je třeba dodat nějaký produkt (nebo jeho část). Spotřeba řídí poptávku. Poptávka je signalizována kanbanovými kartami. To pomáhá vytvořit systém řízený poptávkou (tahem), který minimalizuje zásoby a plýtvání.
Závěr
Principy štíhlé výroby se neustále vyvíjejí. Od jejich zrození před téměř padesáti lety jsou neustále zdokonalovány a dodavatelé softwaru pro ně ve svých produktech vytvořili speciální moduly. Příklady, které jsme si nastínili v tomto textu, ukázaly, že tyto zásady mohou být uplatněny ve všech typech výroby.
Stephen Dombroski, Lukáš Dolníček


![]() ![]() | ||||||
Po | Út | St | Čt | Pá | So | Ne |
1 | 2 | 3 | 4 | 5 | ||
6 | 7 | 8 | 9 | 10 | 11 | 12 |
13 | 14 | 15 | 16 | 17 | 18 | 19 |
20 | 21 | 22 | 23 | 24 | 25 | 26 |
27 | 28 | 29 | 30 | 31 | 1 | 2 |
3 | 4 | 5 | 6 | 7 | 8 | 9 |
22.5. | Cloud Computing Conference 2024 |
5.6. | IT mezi paragrafy 2024 |
20.6. | Cybernity 2024 |
Formulář pro přidání akce